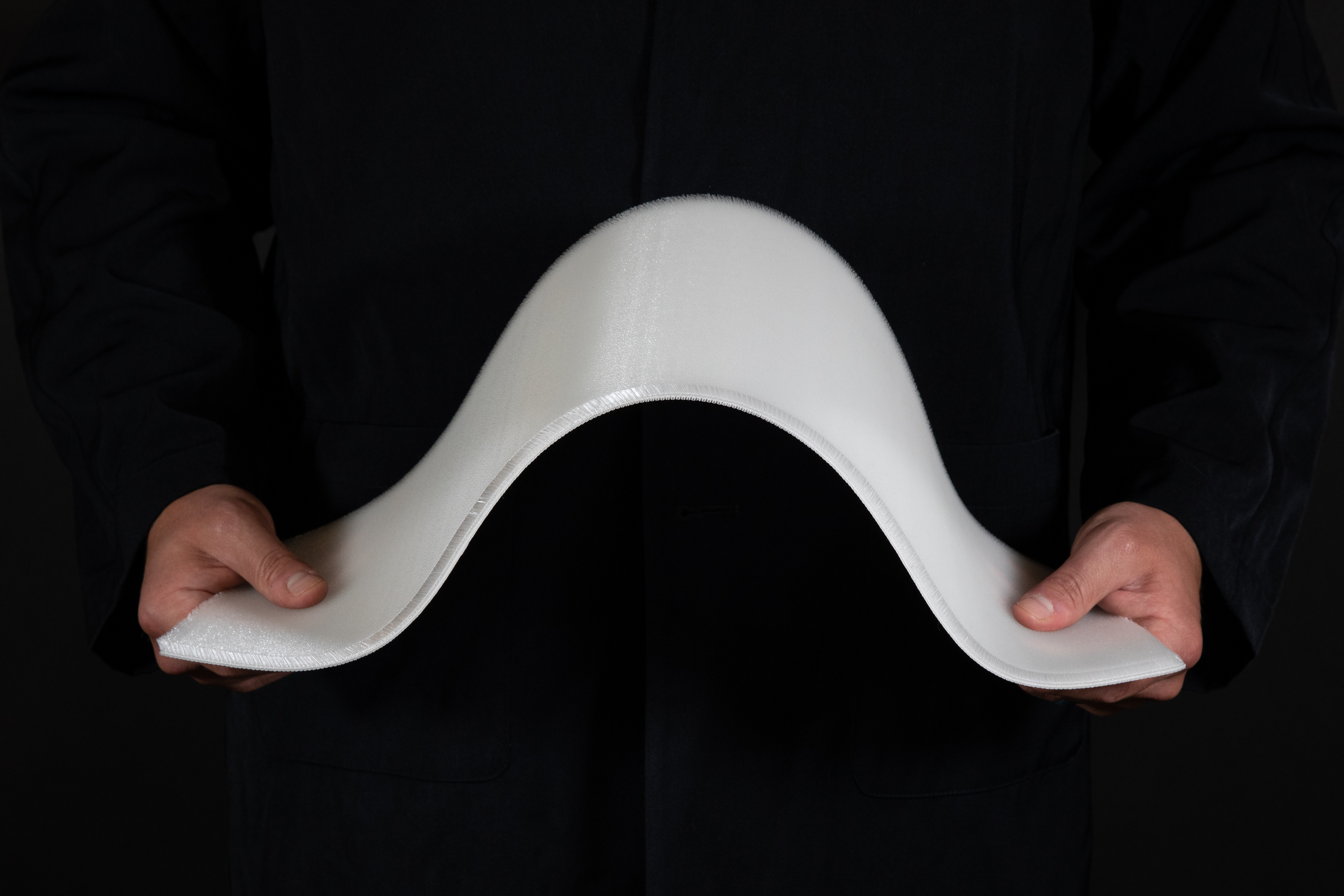
Our aim for inventing PolyBrush™ was clear: develop brushes for linear conveying that maintain consistency, speed, and direction while safeguarding parts from damage or entrapment. Unlike previous rubber or urethane-based products with glued fibers, our approach began with replicating similar geometry and bristle spacing to ensure identical performance. However, recognizing differences in design, material, and production, we adapted our process to ensure seamless integration with existing conveyor systems. Our densely packed brush design seamlessly complements current setups, offering ease of customization and simple adherence to machine surfaces, all while ensuring optimal performance in tandem with traditional products.
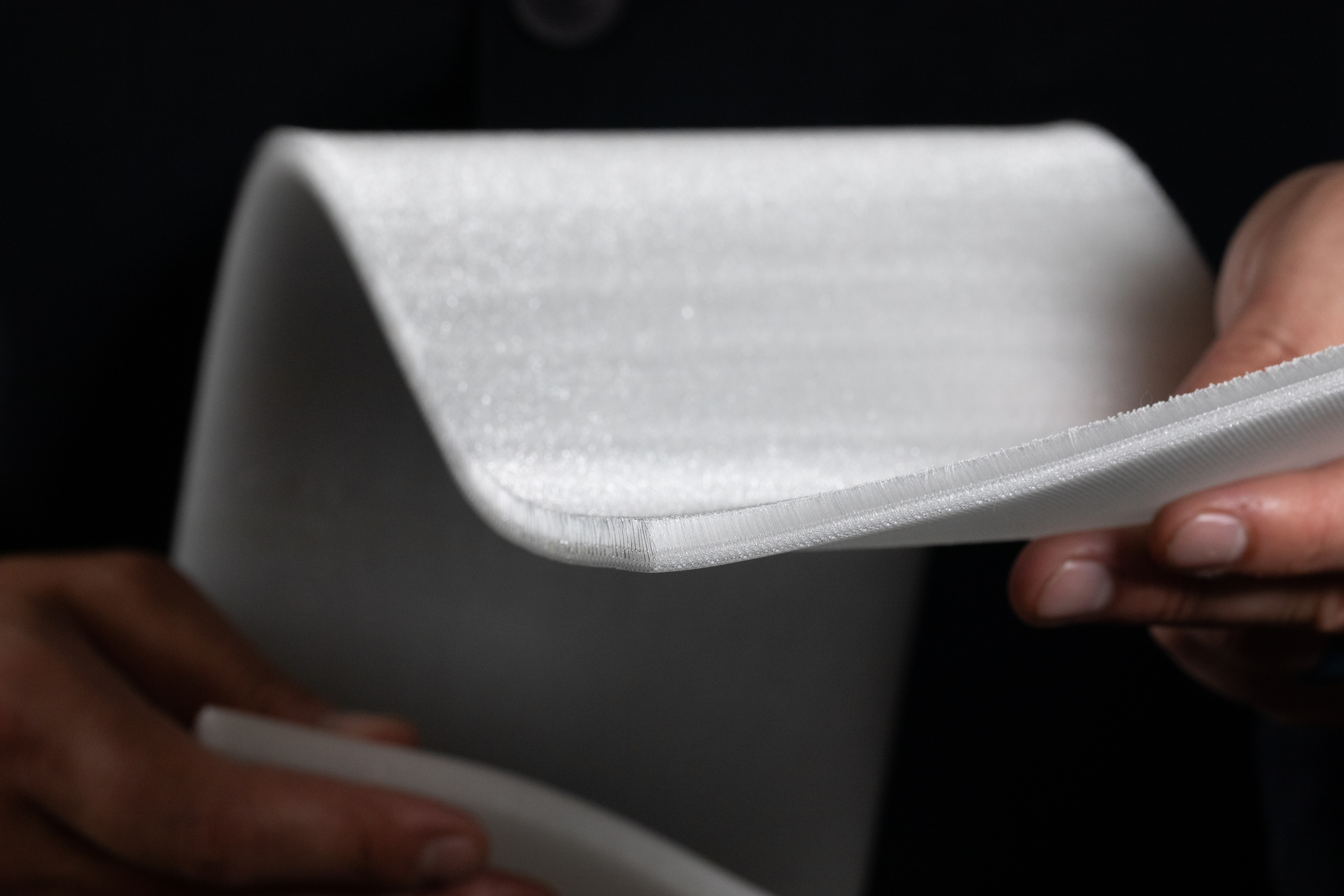
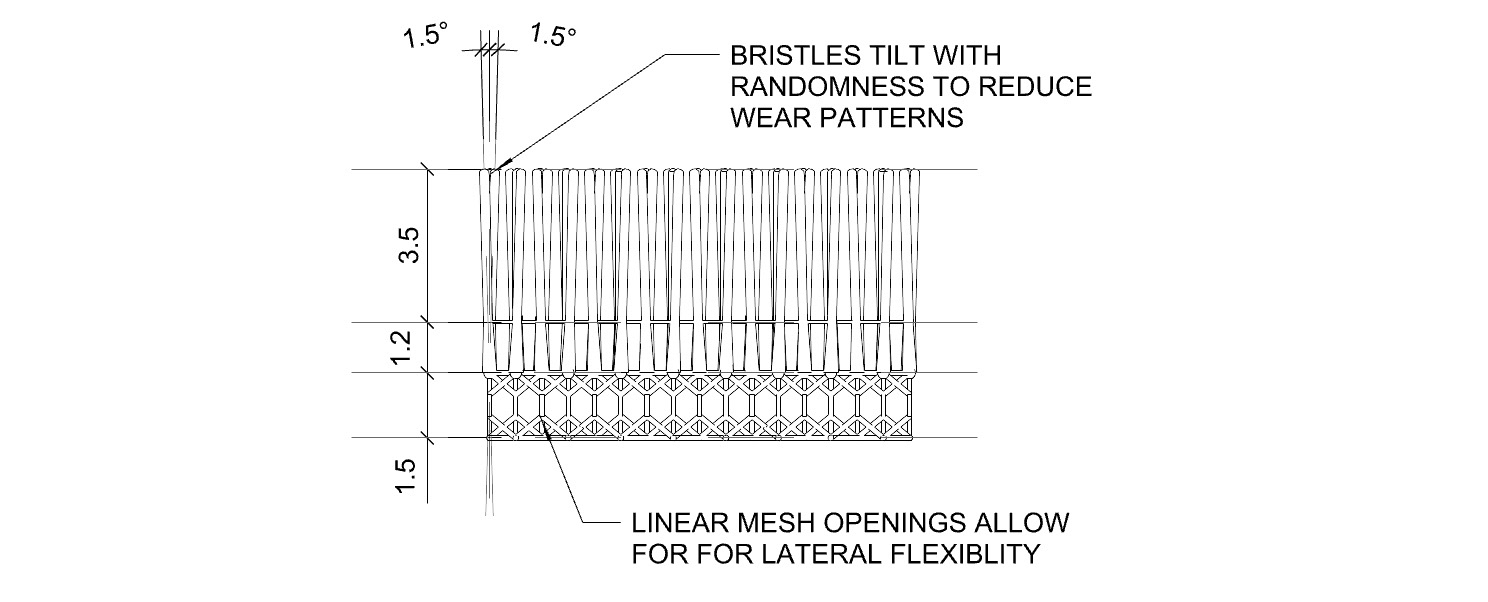
Crafting fur and fur-like structures presents unique challenges. Achieving the required density poses both computational and practical hurdles, demanding clean coding to manage file size without compromising design fluidity. Moreover, achieving the desired tactile and visual qualities necessitates striking a delicate balance between randomness, spacing, and element size to prevent clumping post-production while preserving the intended aesthetic and texture. Our innovative approach tackles these challenges head-on, pushing the boundaries of what's achievable in additive manufacturing.
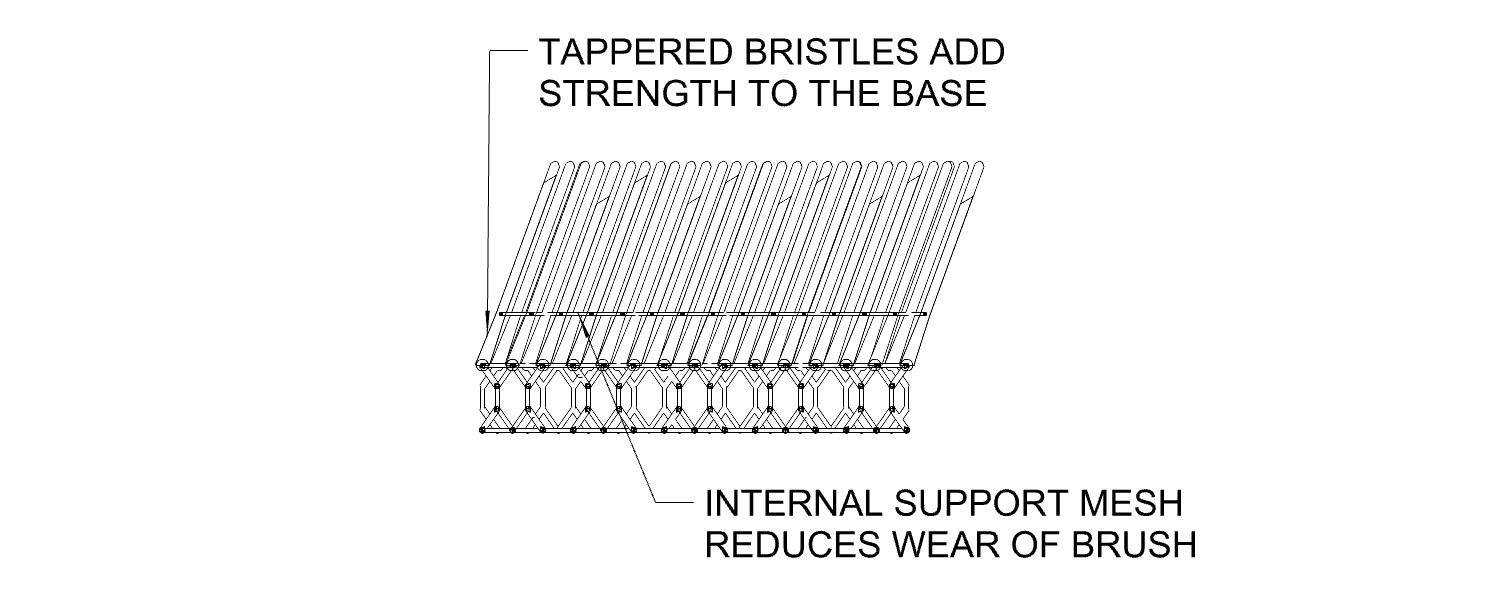
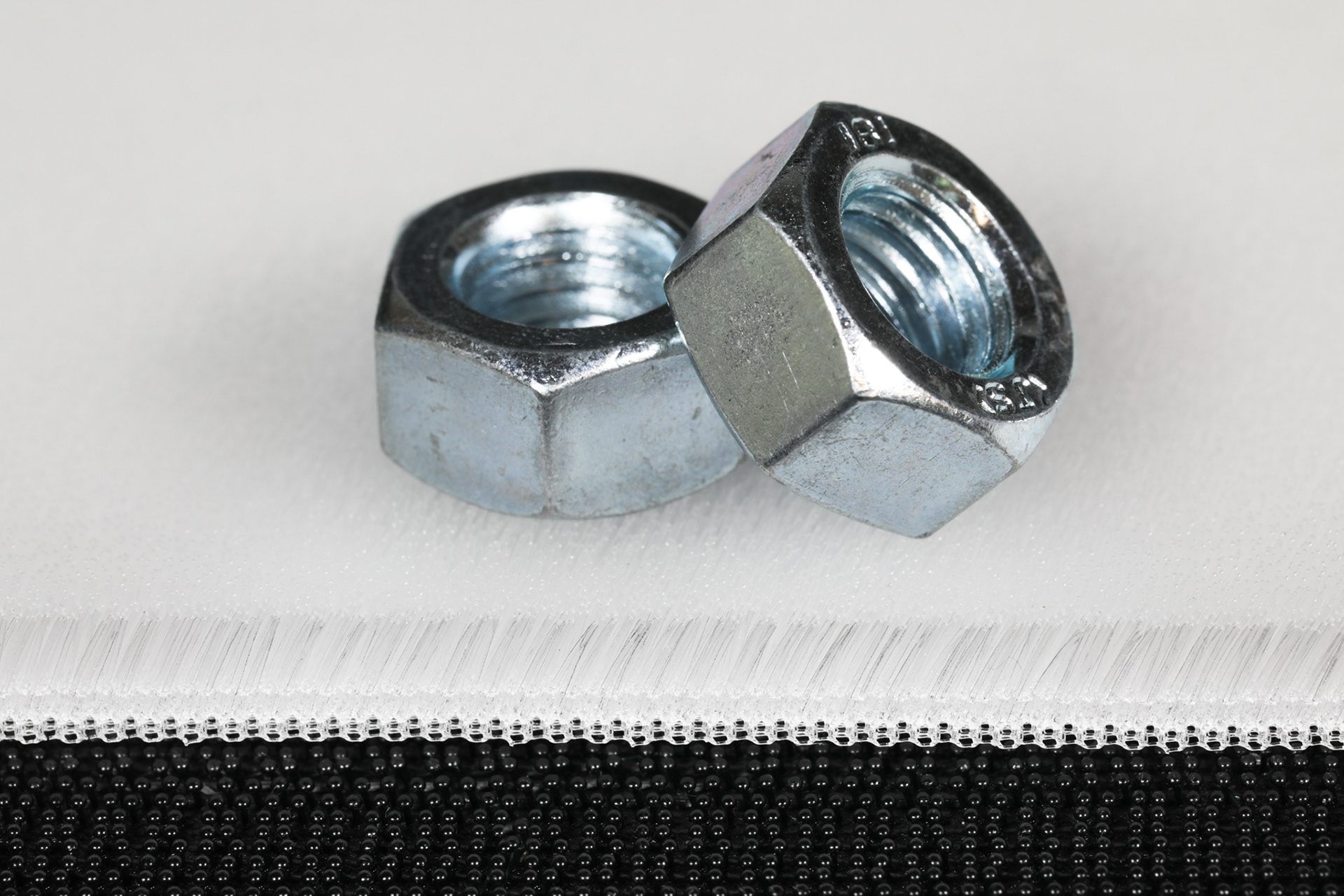