Working in collaboration with Origin Laboratories (now Stratasys), this project’s goal was to design and develop a 3D printed midsole for a casual running shoe. There was a client emphasis on parametric design that needed to be set up for fast micro-adjustments as more and more 3DP iterations continued to come off the printers. This lattice structured midsole was created by formulating a 3D voxel cell that would be able to repeat and adjust in reaction to a pressure map of the foot along with other added outlier data points that were factored in. Additionally, the client was interested in creating a fully functional knit upper to be bonded to the midsole. Working with product developers and factory engineers in Asia, various maps of stiffnesses, material thickness, and knit patterns were collaborated on which allowed for getting good sample prototypes made for fit testing.
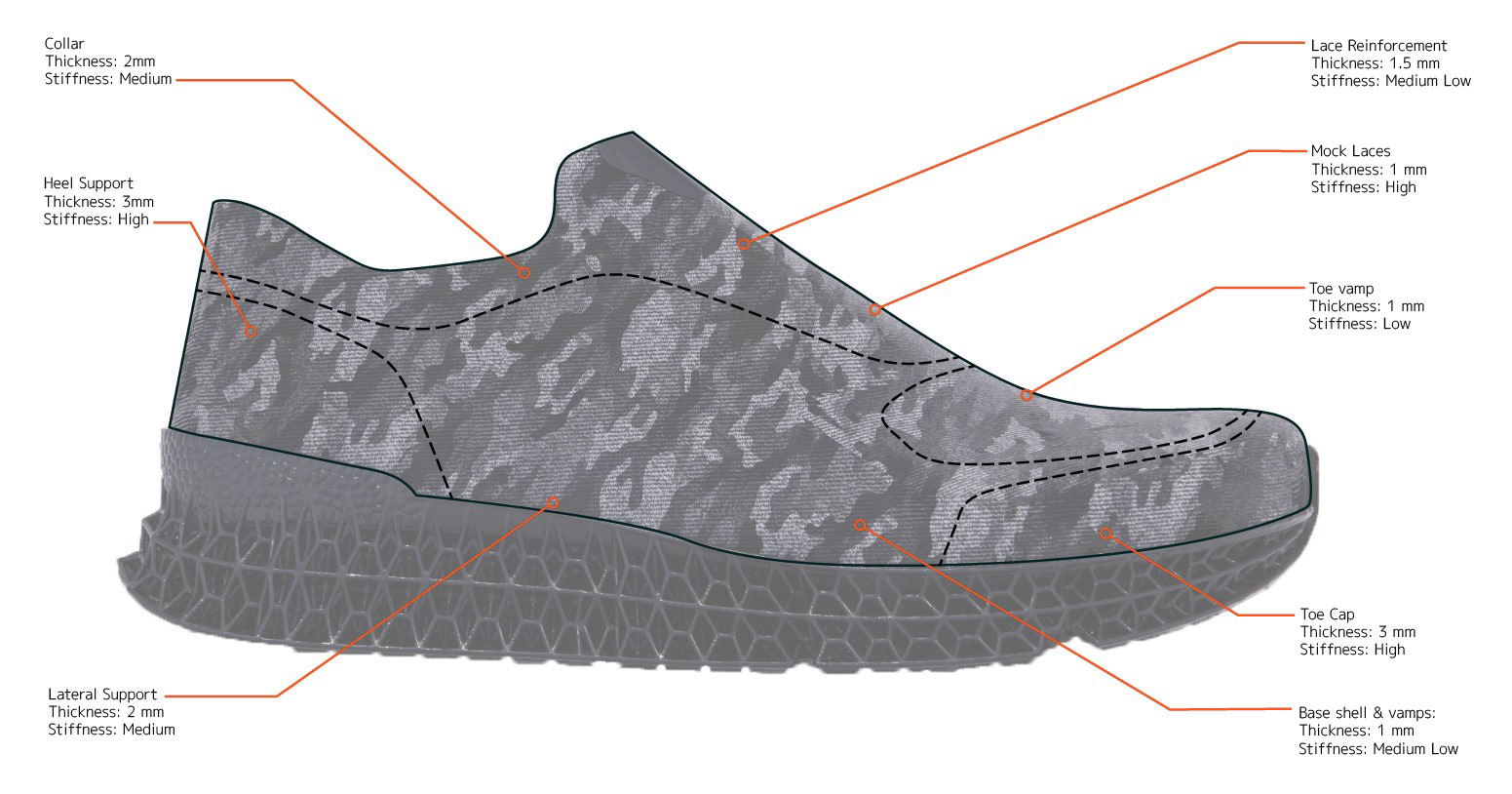
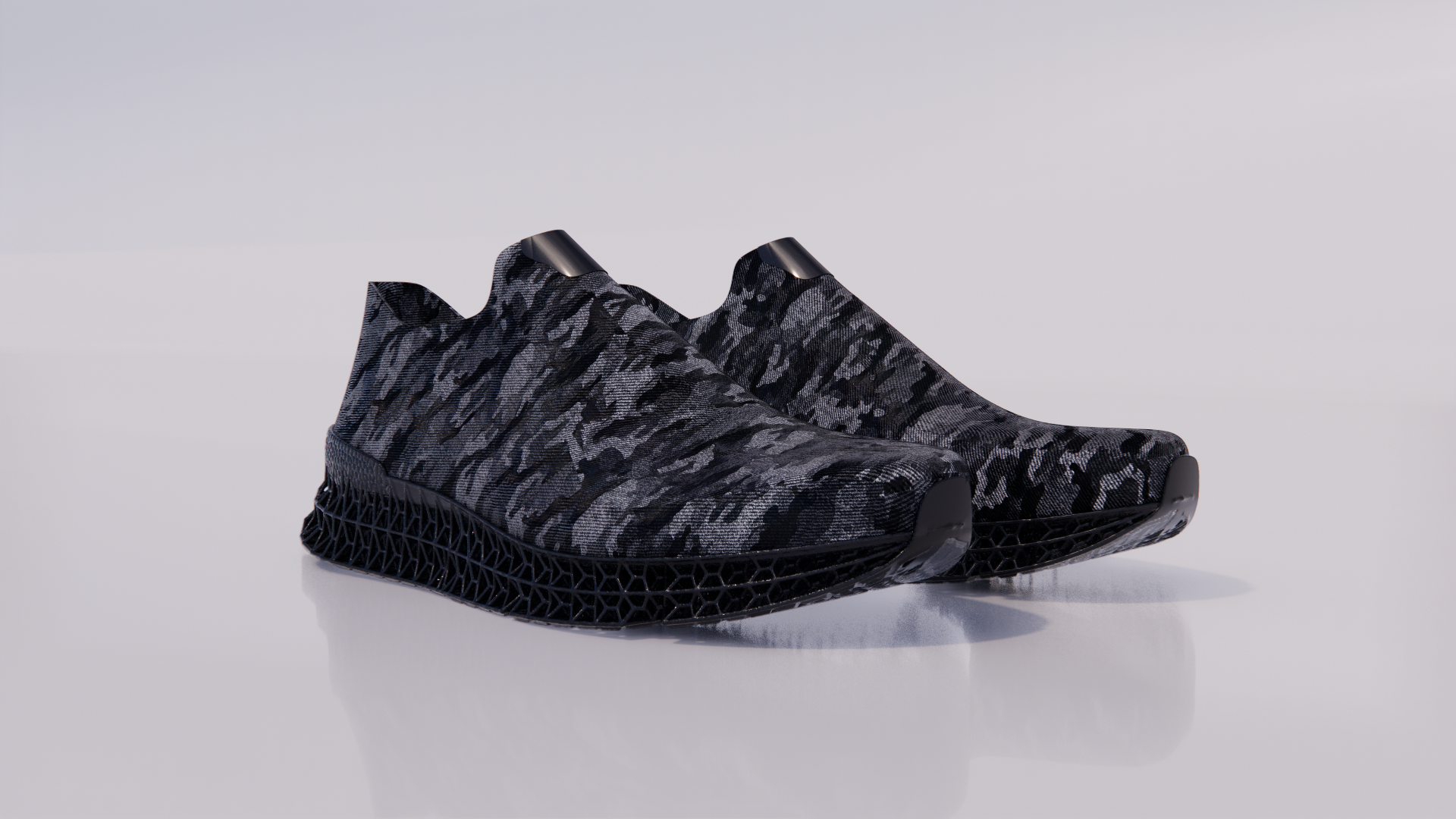
FEA testing specific material tolerances on a resin 3D printer proved to yield interesting and informative results which allow us to try out unique adjustments in geometry for vastly different results. Testing the rebound, compression of the lattice structure informed decisions on where and how to populate the voxels within the midsole. Voxel studies were performed depending on scale, thickness, and hexagonal orientation. The structural properties of each cell depend on the beam length and orientation, not the cell shape. Each lattice cell has different structural properties in the XY and z-direction. The more specified vertical areas will sheer more than compress. Thicker more vertical beams will be substantially stiffer while more angled and thinner will compress more.
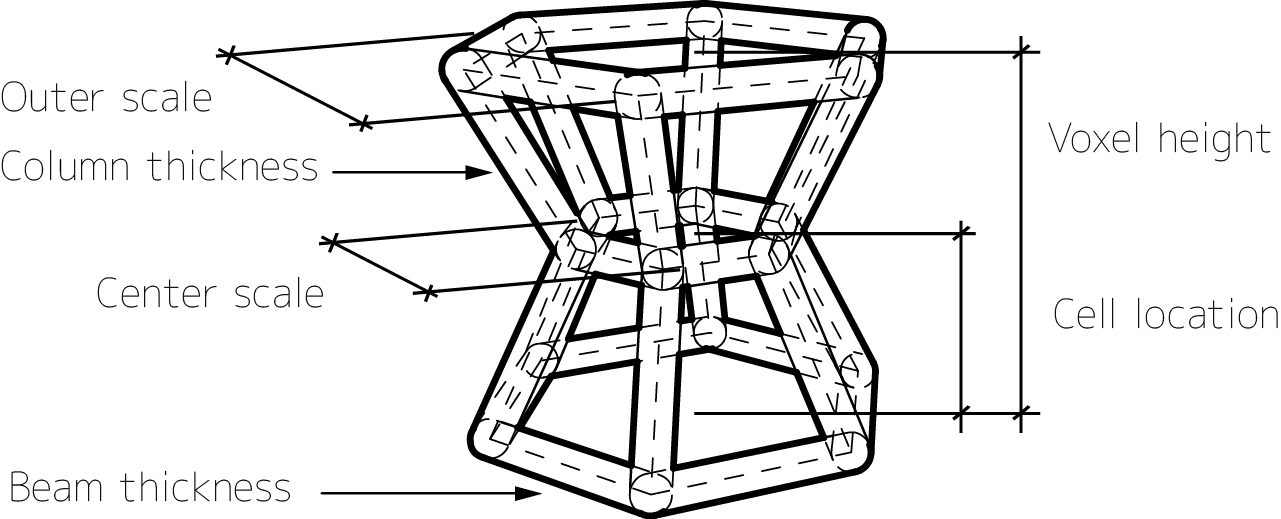
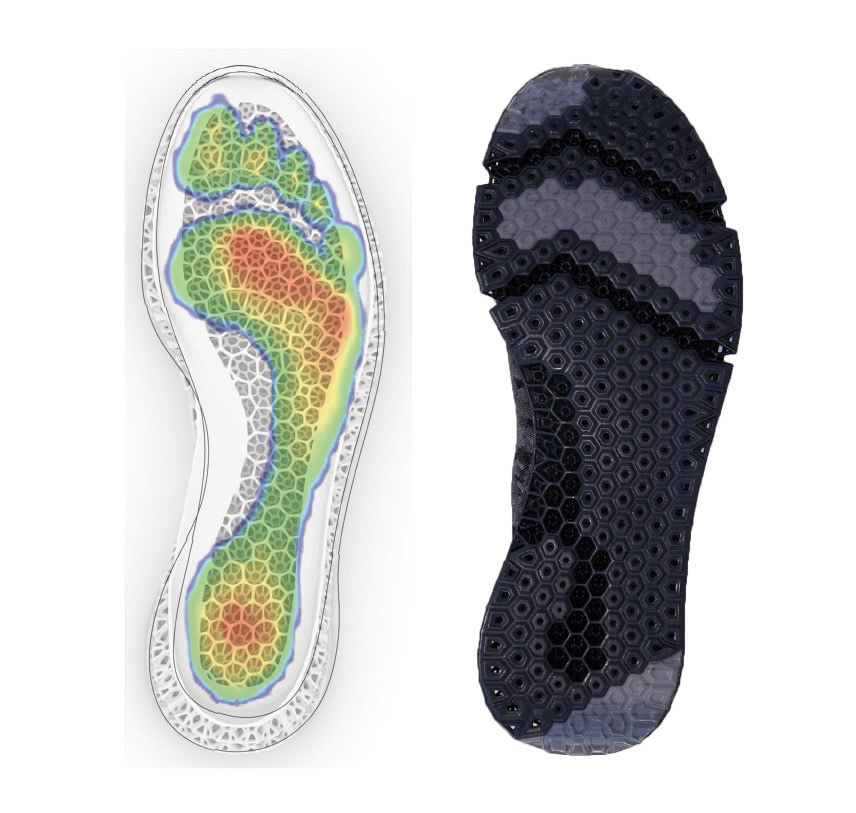
A variation in stiffness was built-in with the cells simply by altering the inner cell size effectively changing the angle of the vertical beams. The outsole lugs match the complex lattice pattern while also incorporating central perforation voids for UV curing and flex grove locations. The triangulated mesh is mostly made up of morphed hexagons, if the triangles are close to equilateral the result is a Voronoi. Therefore, the cell size was easily variable based on a pressure map and more additional control over the cells. Instead of morphing a grid, triangulation of a cloud of points was done to have much denser and sparser areas that wouldn’t be achievable by morphing a 2D grid. Depending on the application, it was found that usually, it’s better to make a lattice skin on the surface and morph the beams to connect to the skin. If the load is normal to a curved surface it’s usually better to morph between surfaces as cells are oriented to the load.
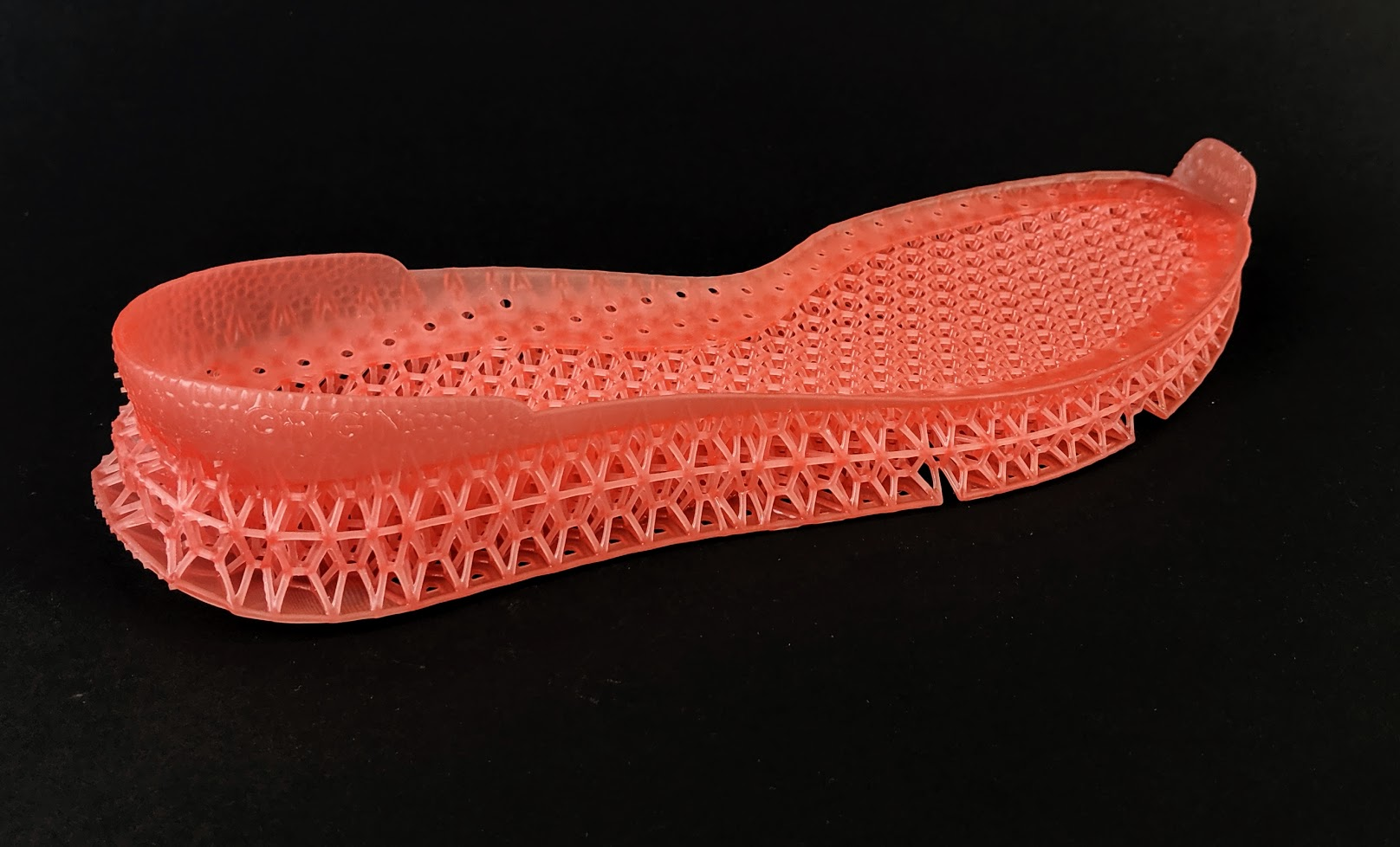
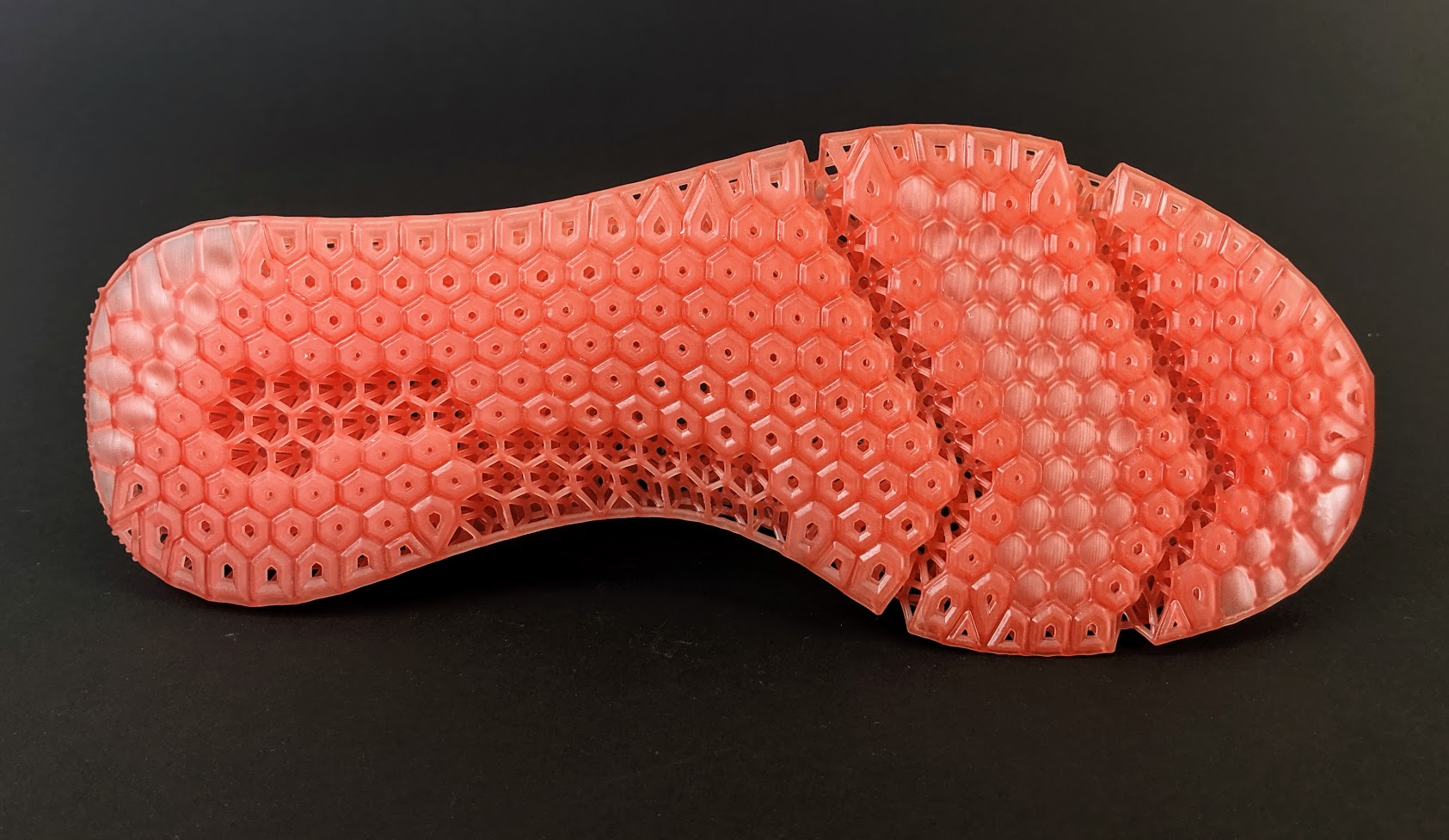
The main inspiration for the shoe design was found in analyzing the form and function of the footbed structure of a Velox Bird (Roadrunner) This speedy and lightfooted bird gracefully covers a lot of ground quickly because of its lightweight and how well the feet rebound off the ground. We wanted to try and emulate this.
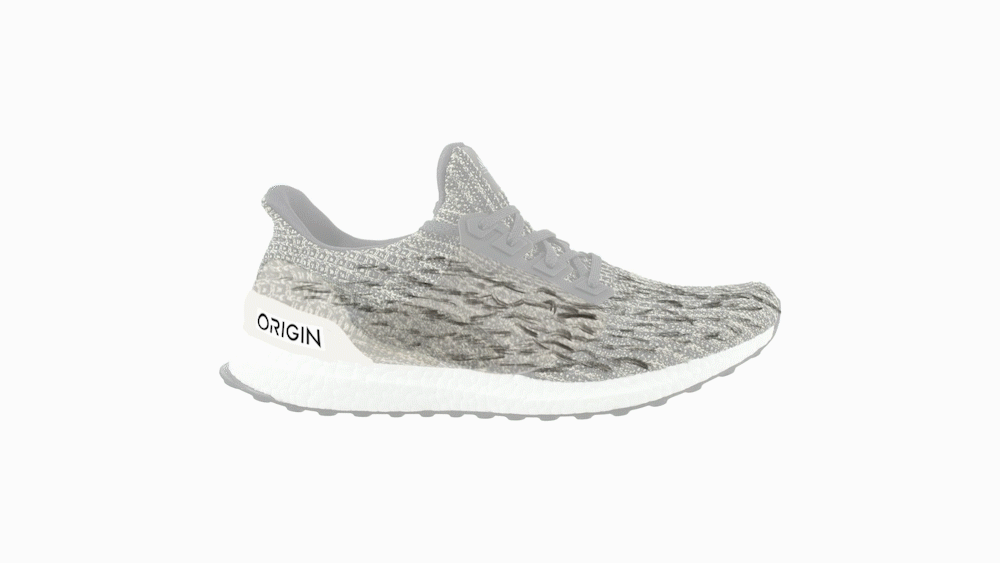
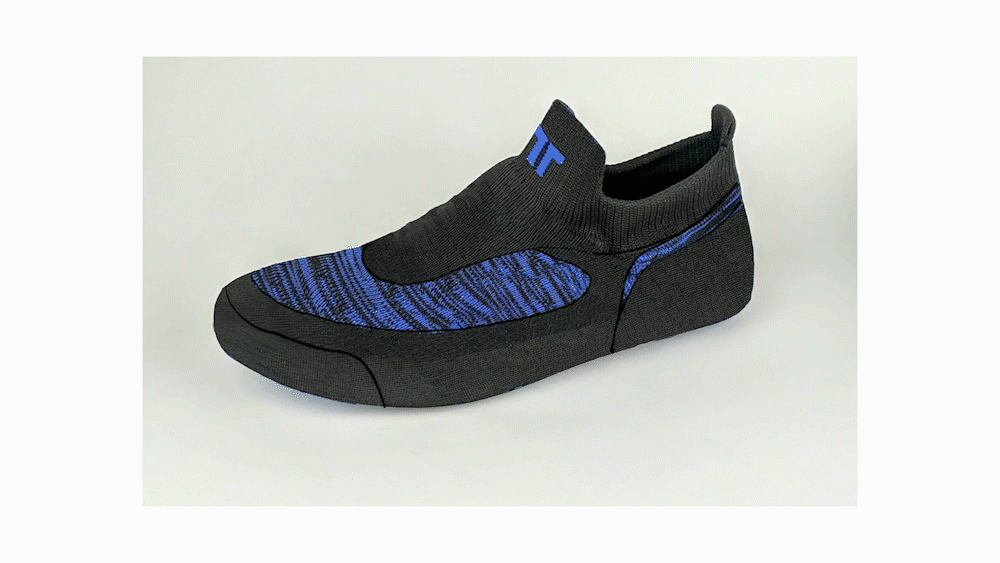
Once the midsole was in a good place, we began testing different knit patterns for the upper. We worked with factories in Asia to establish a look that would work well with the form we established.
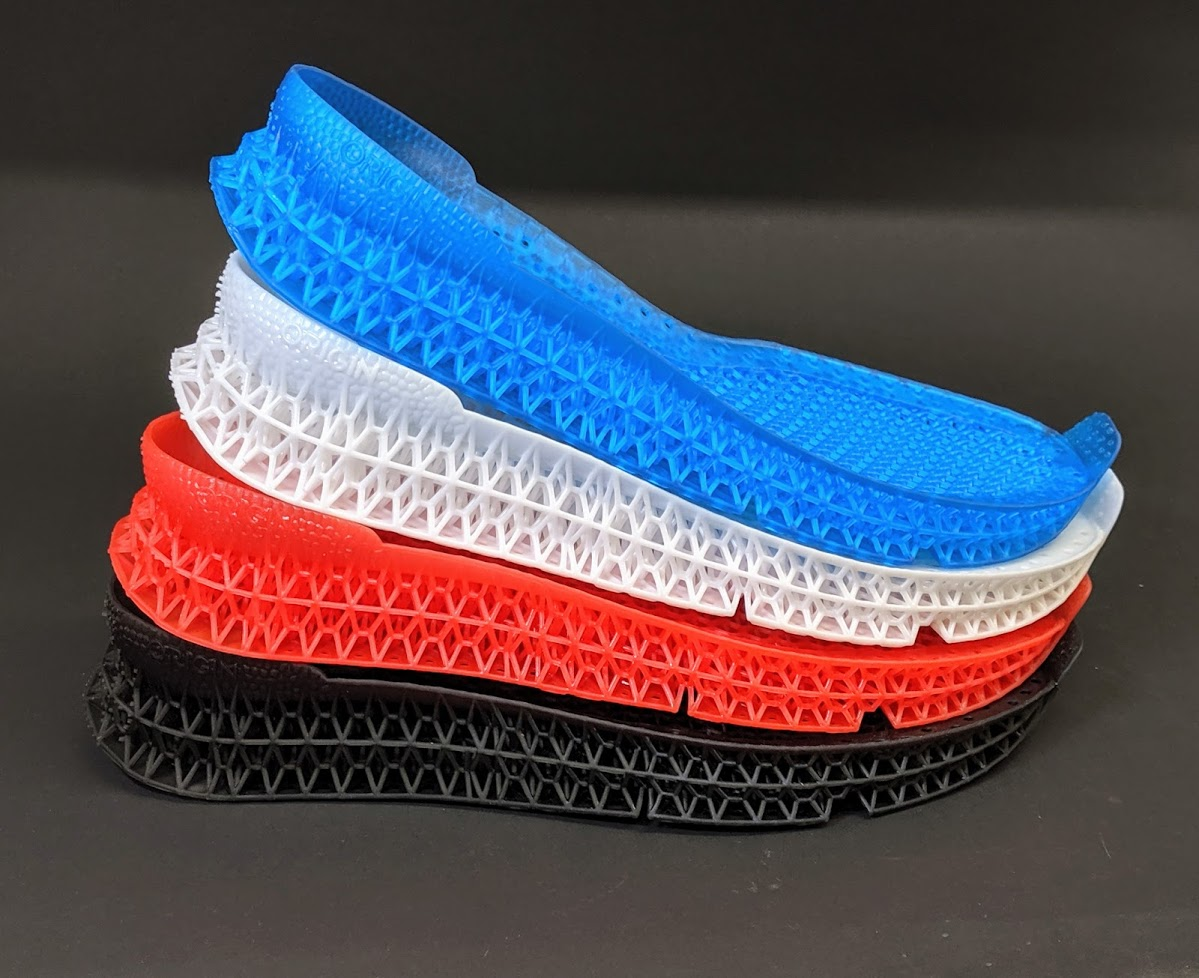
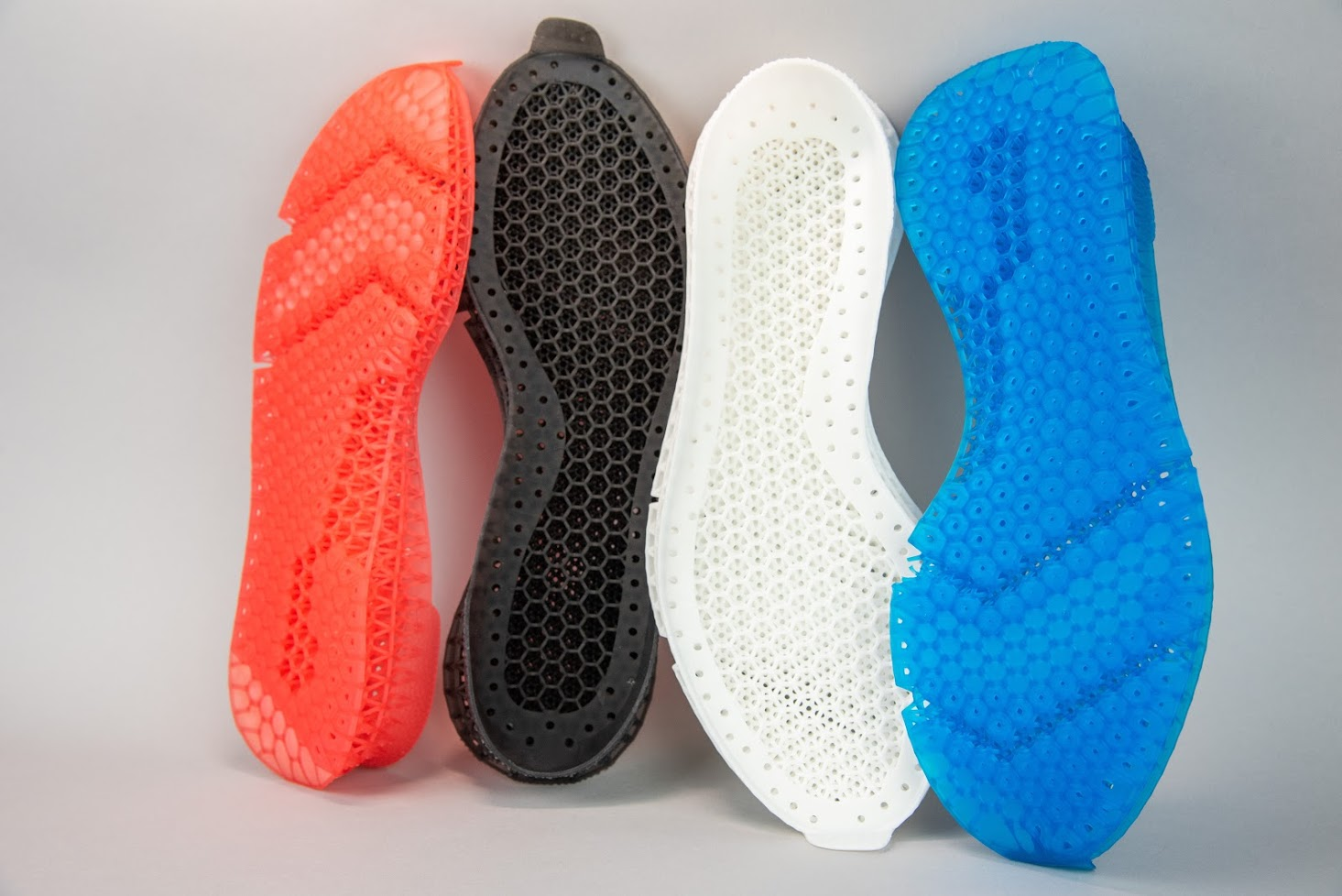
Process Images
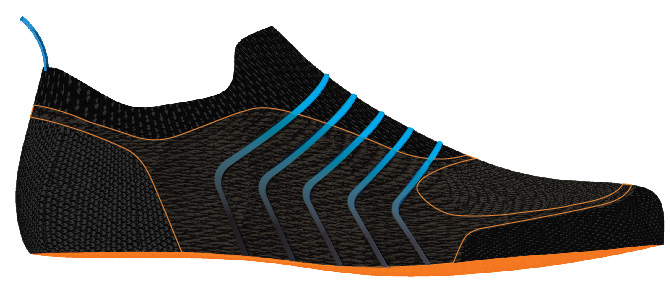
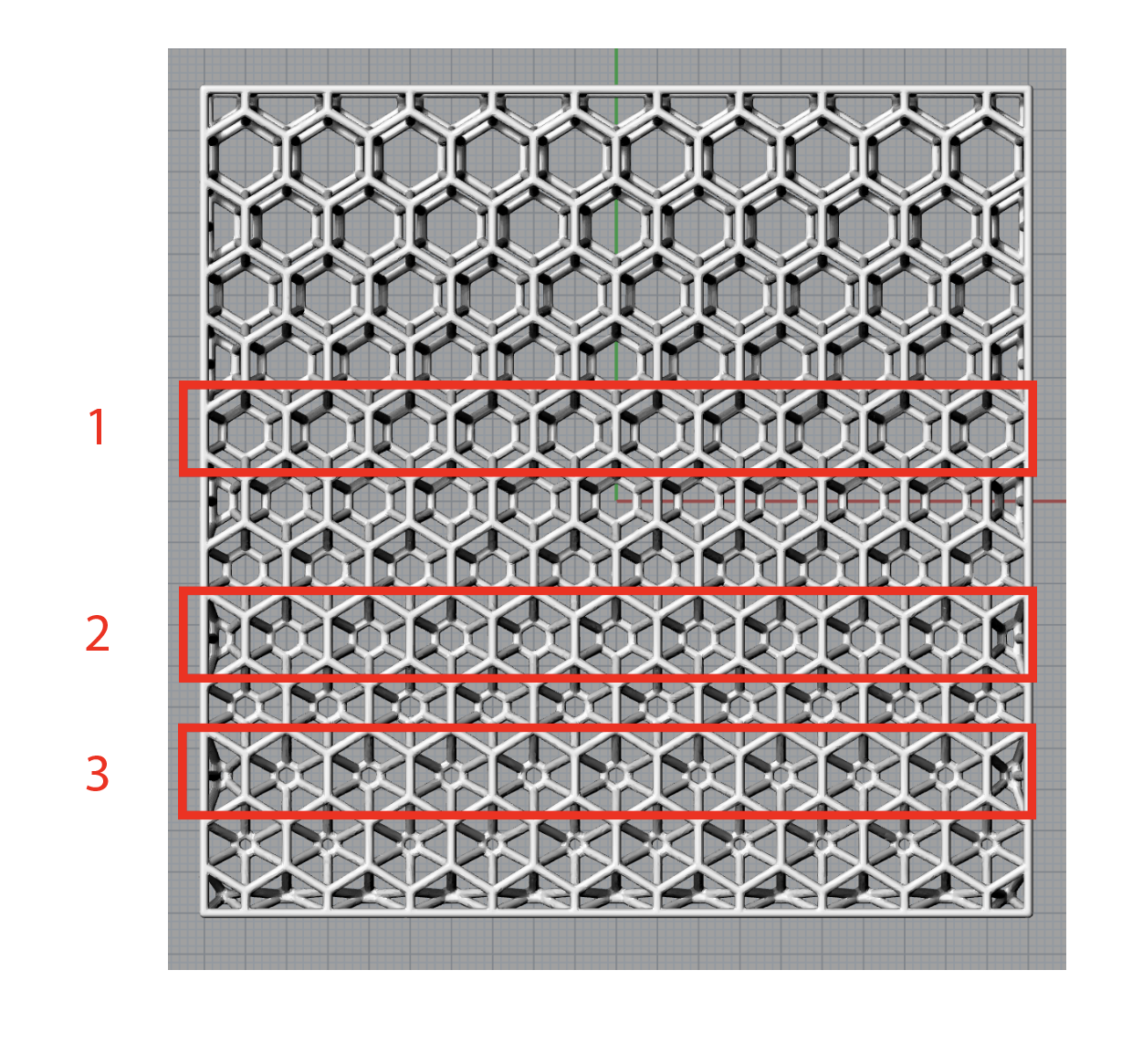
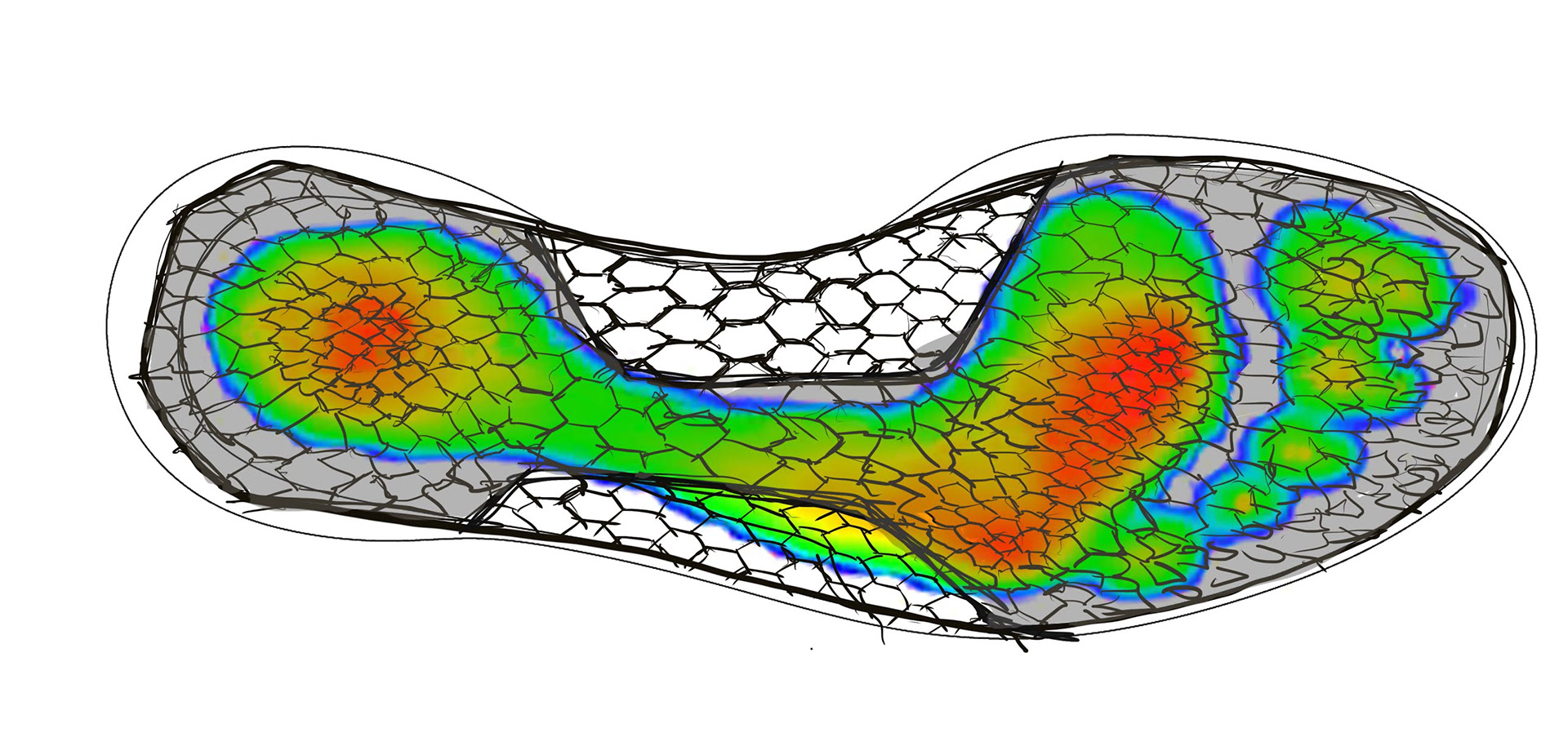
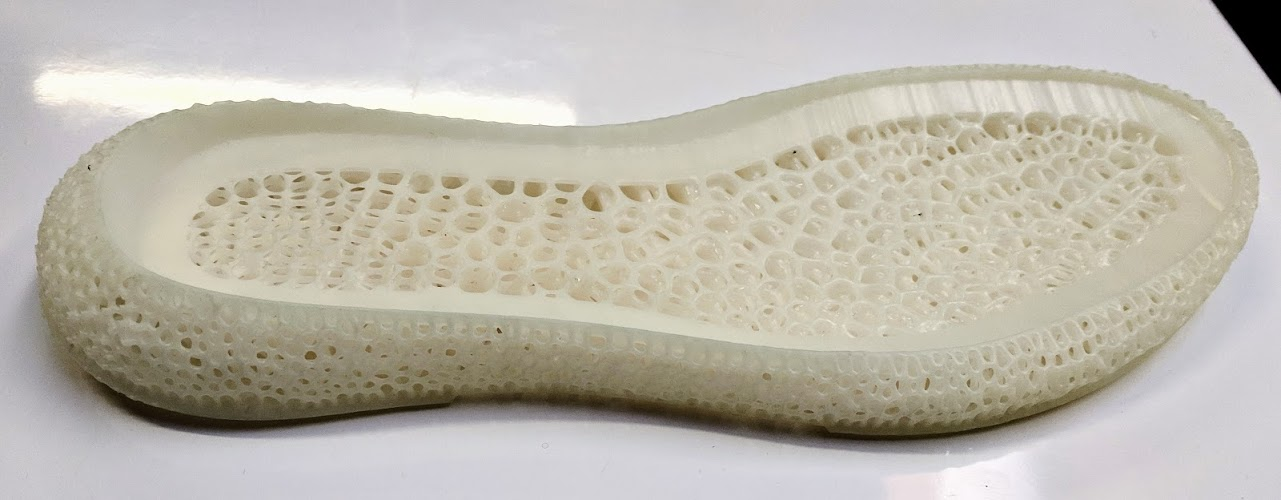
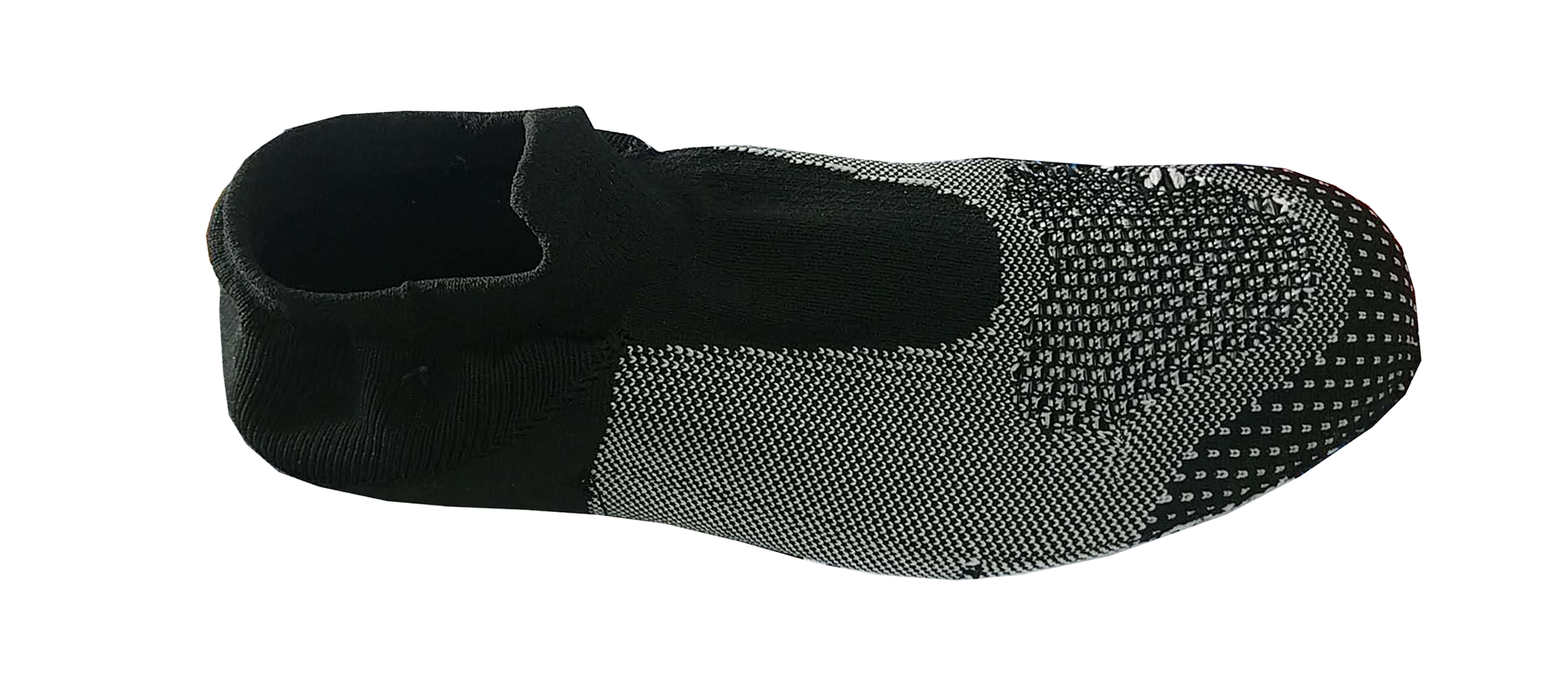

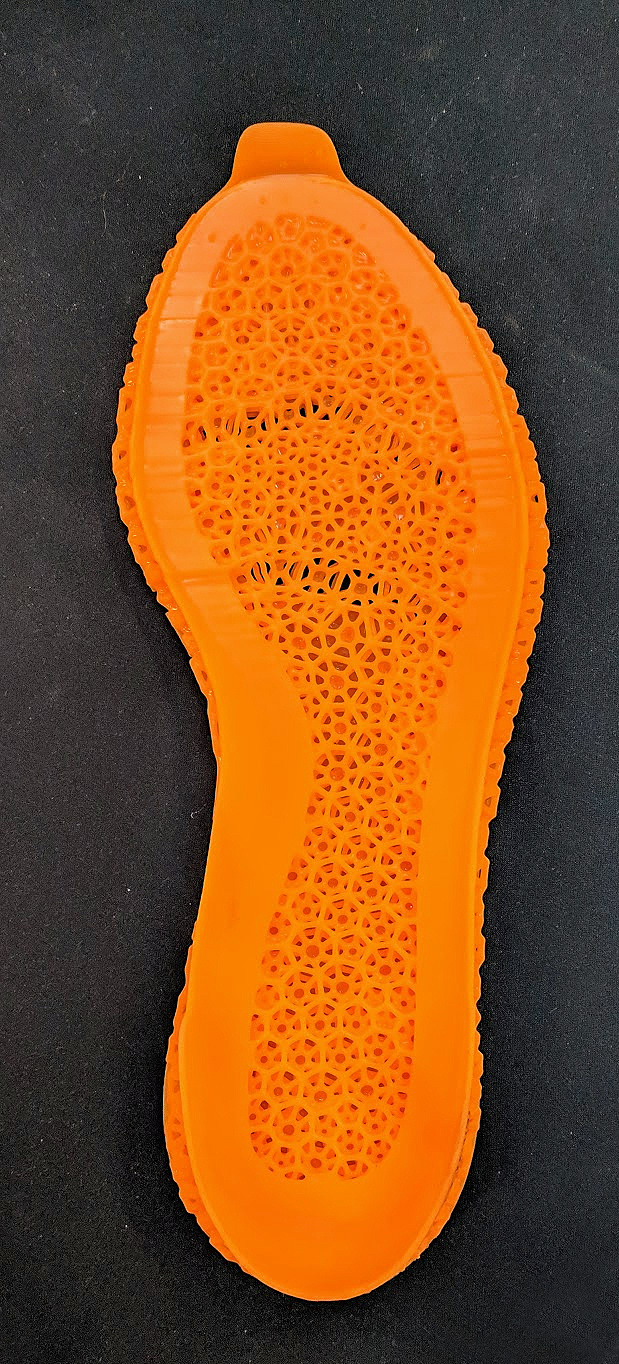
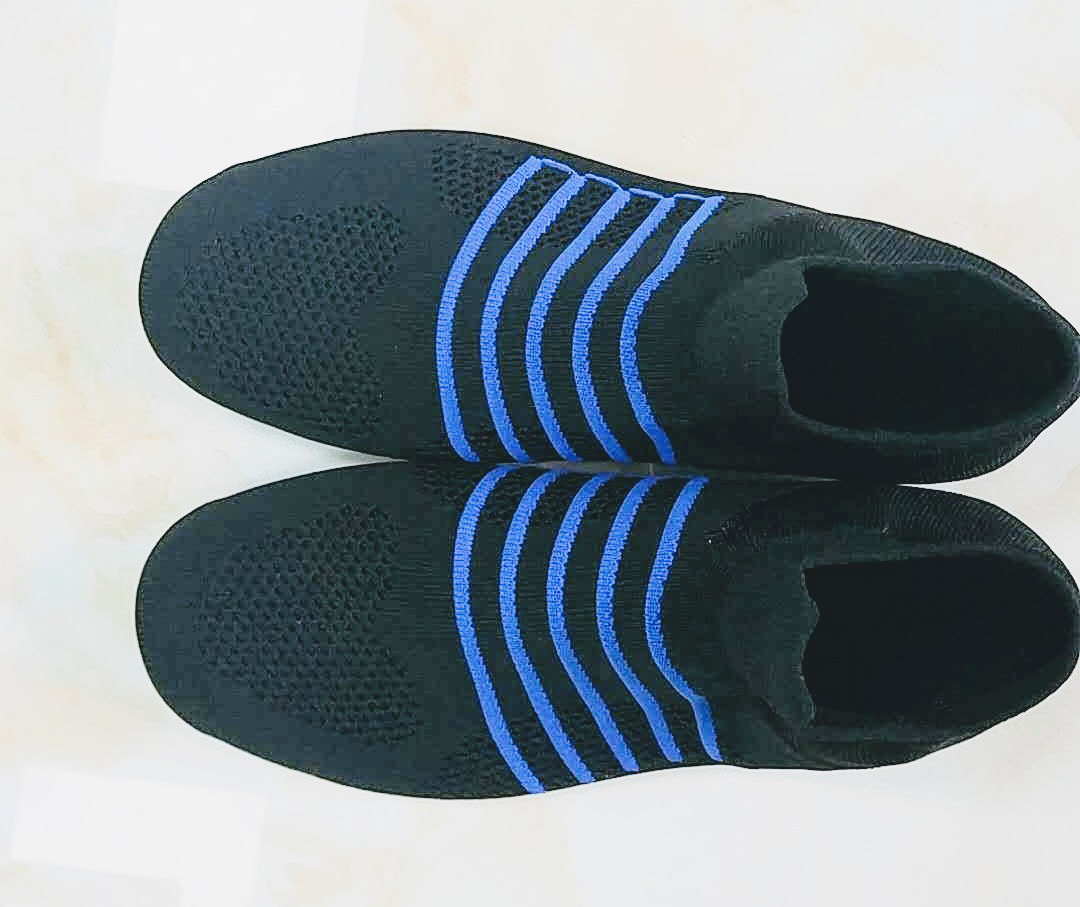
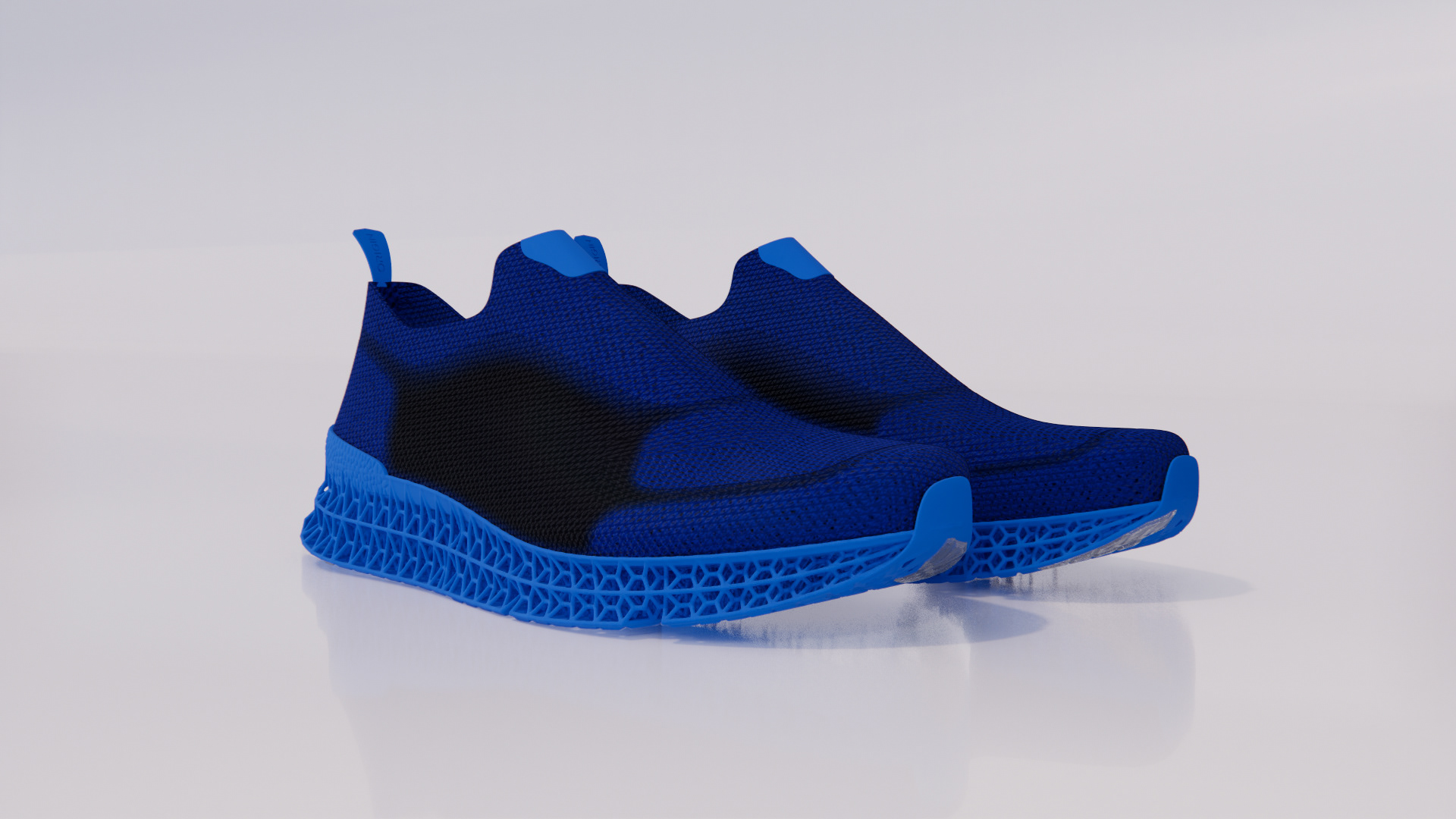
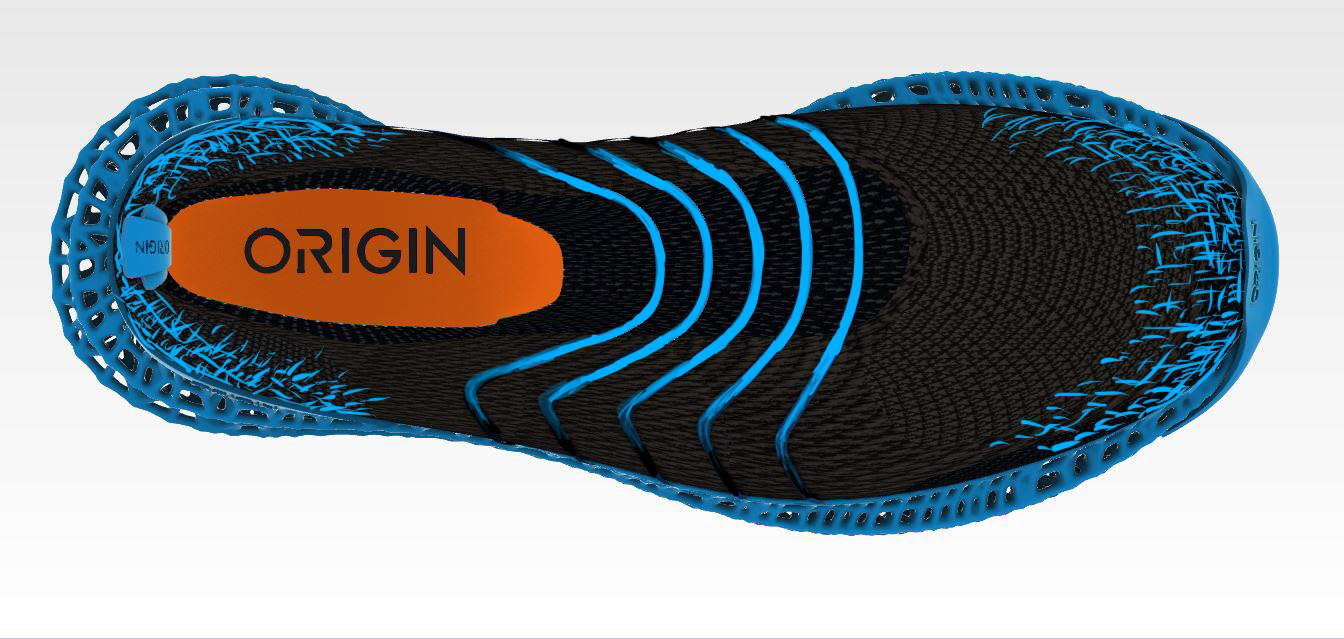
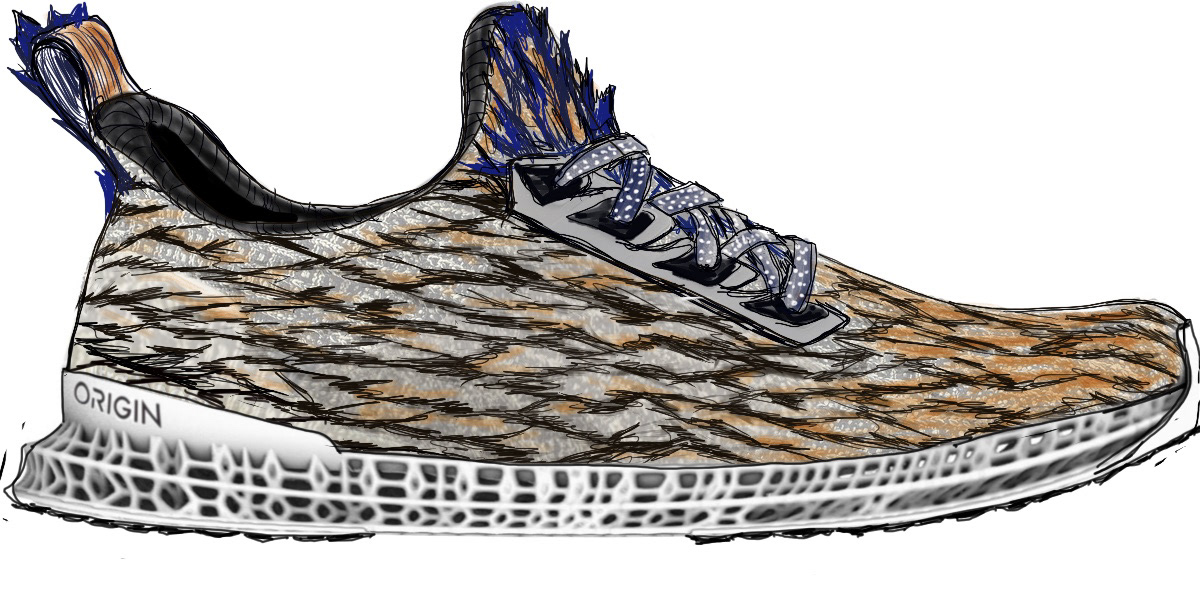
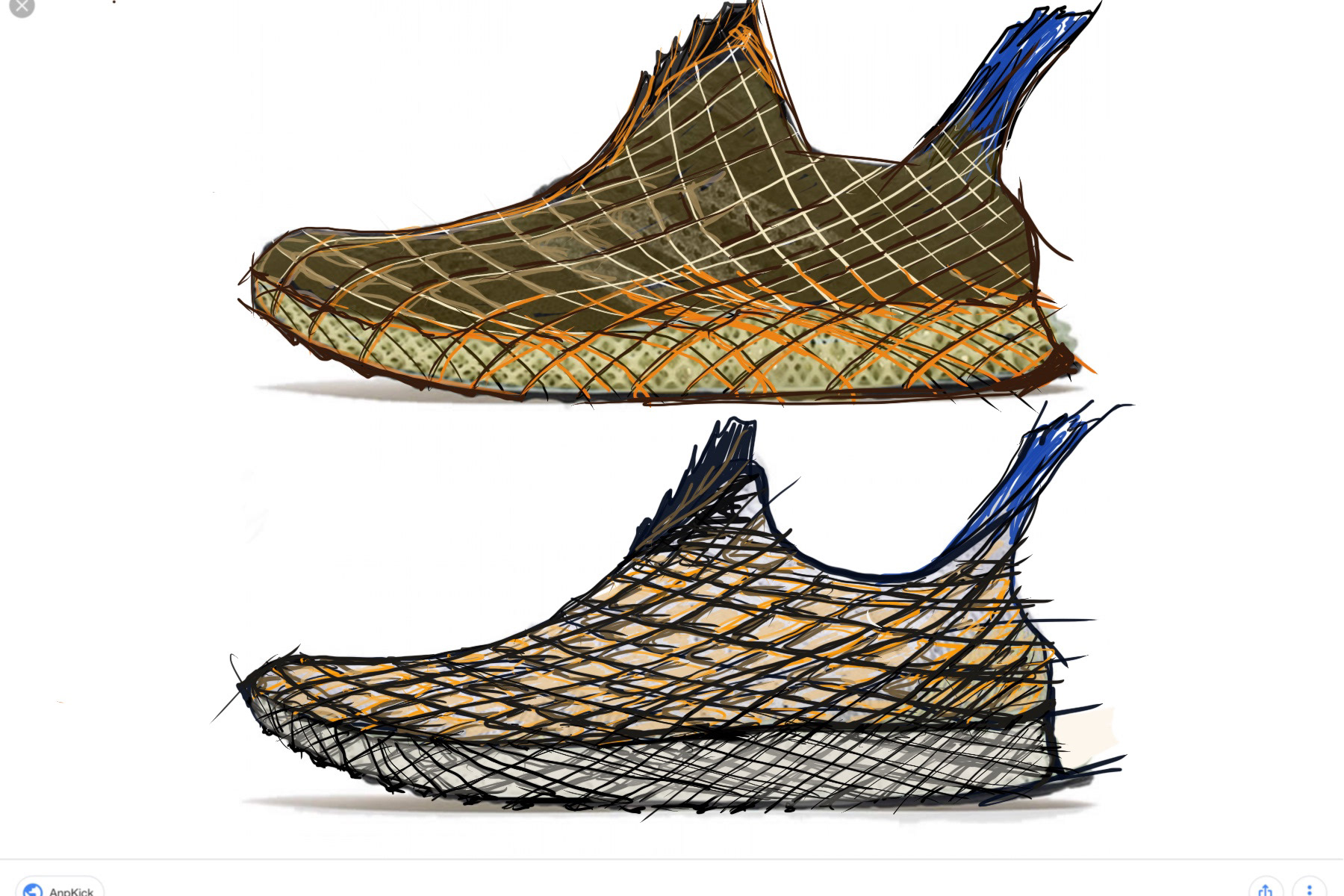
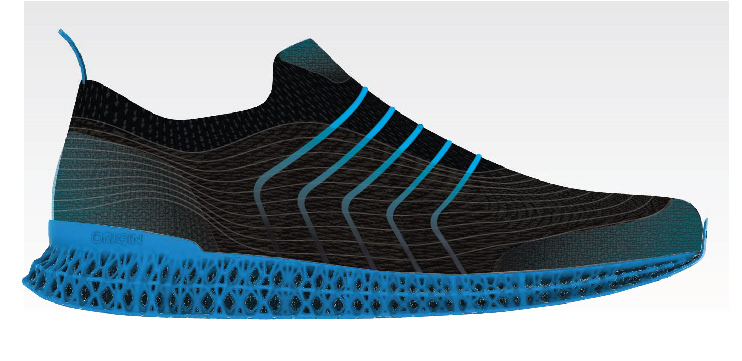
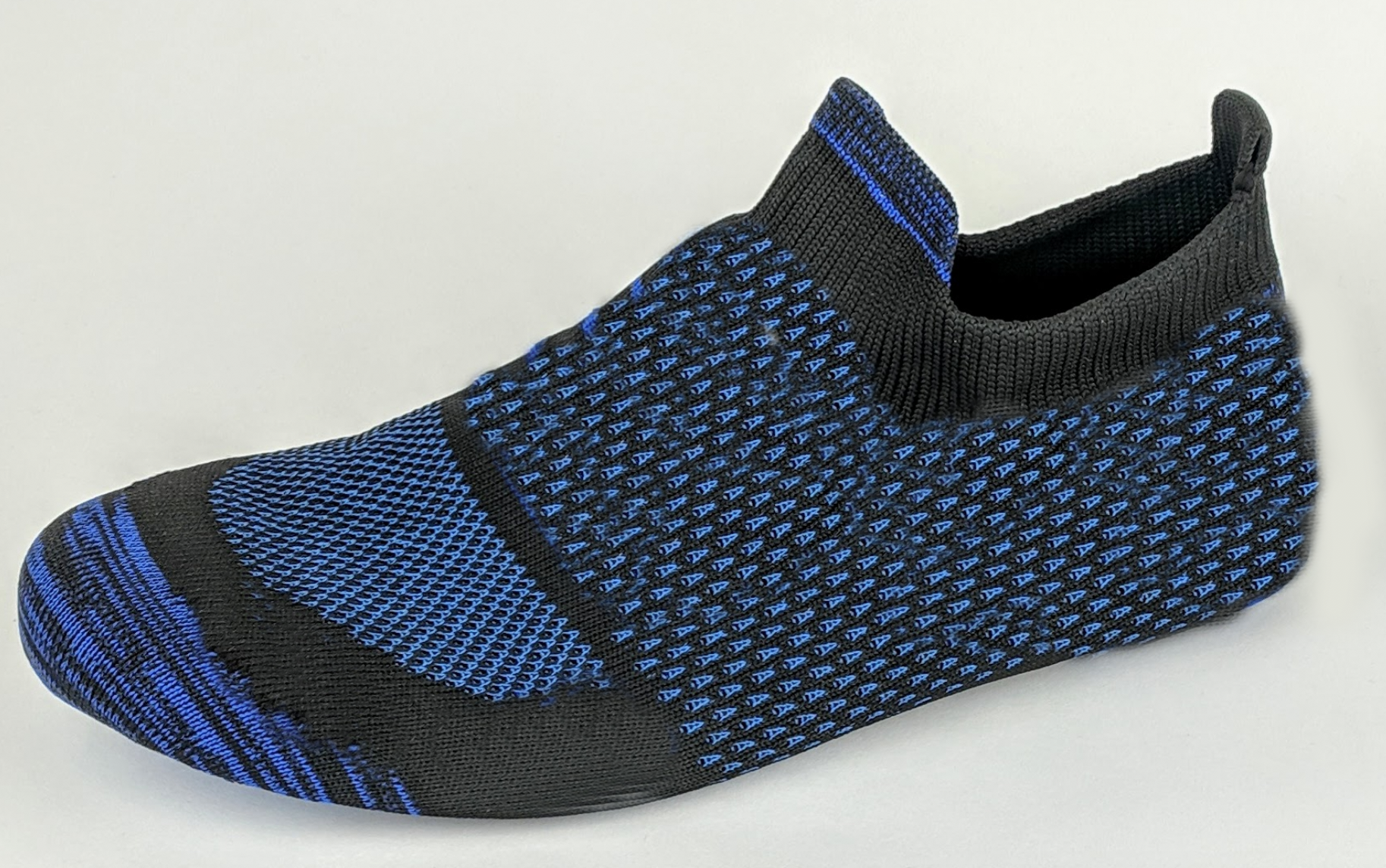
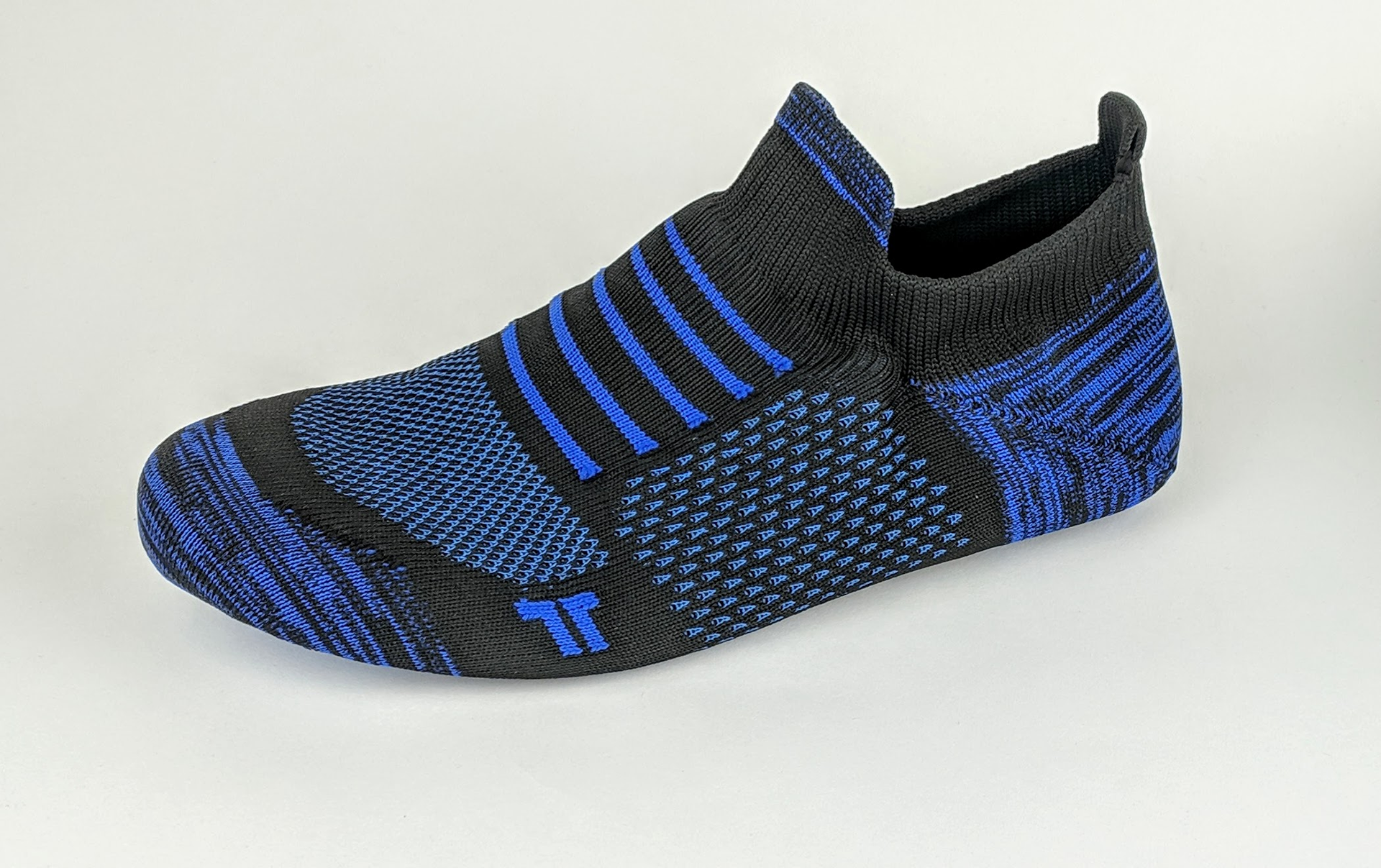
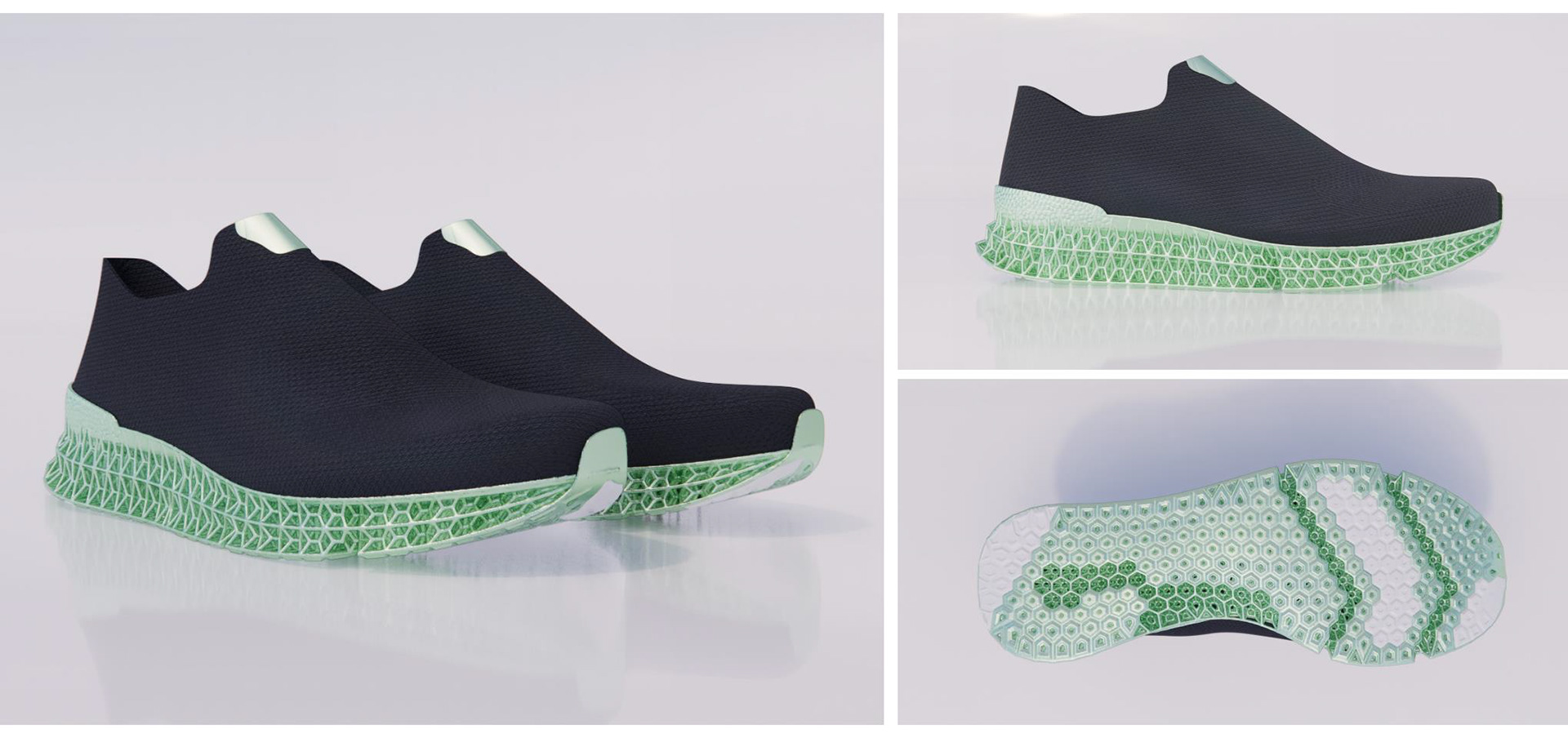
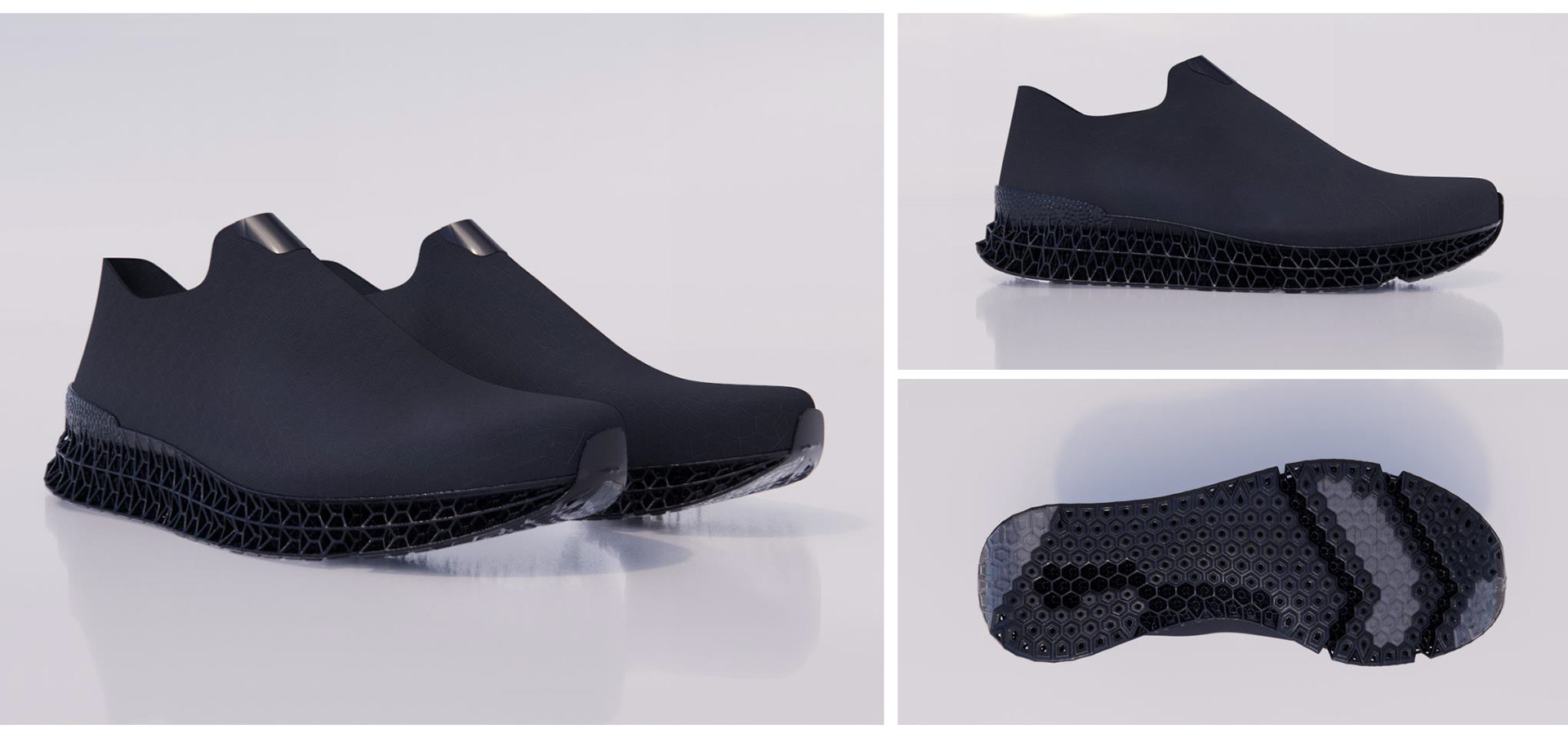
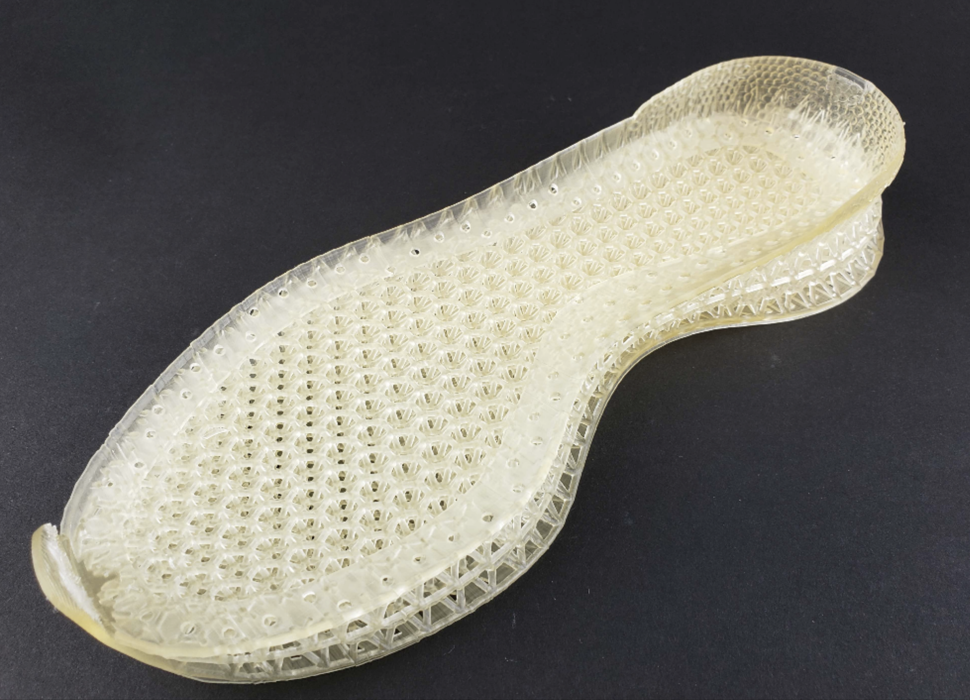
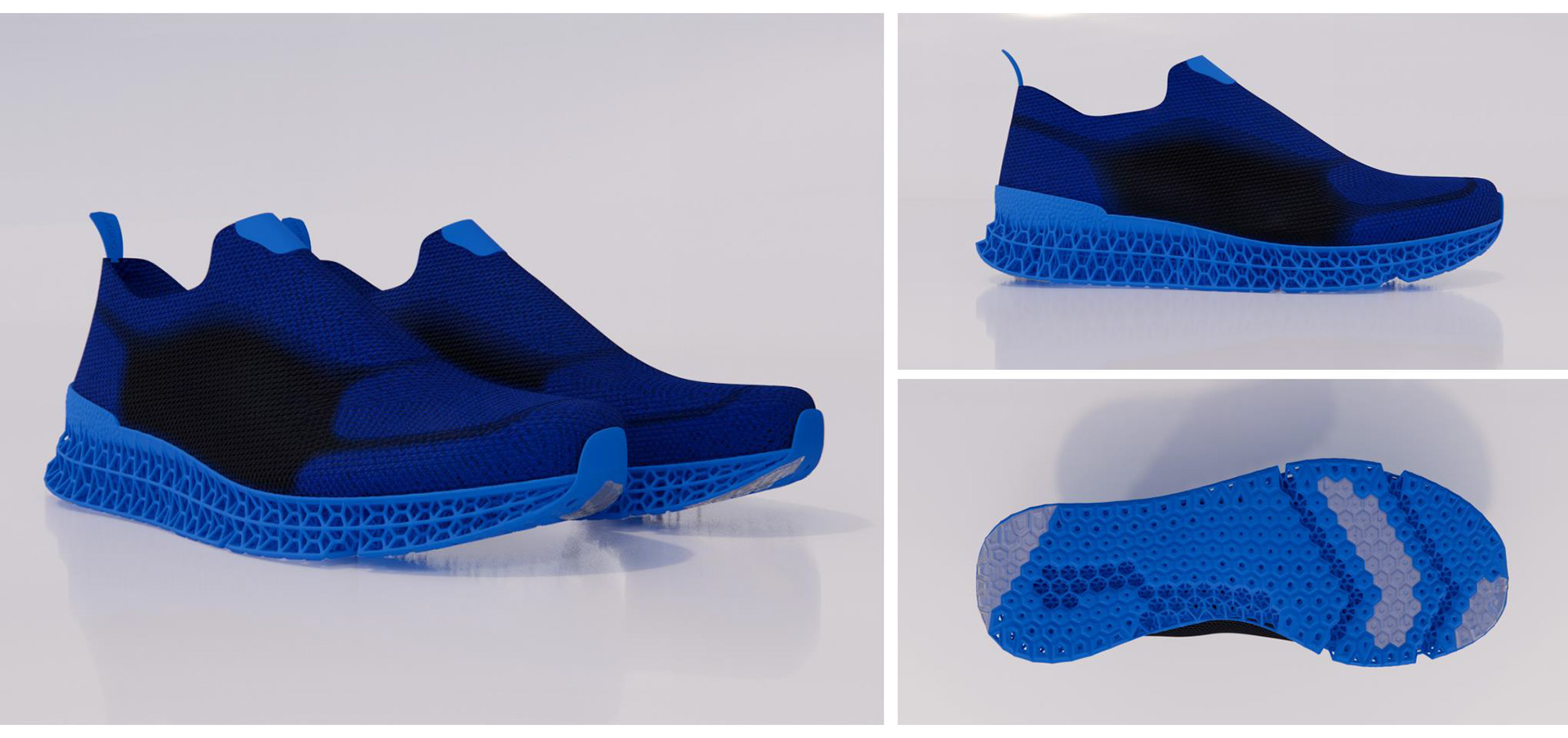
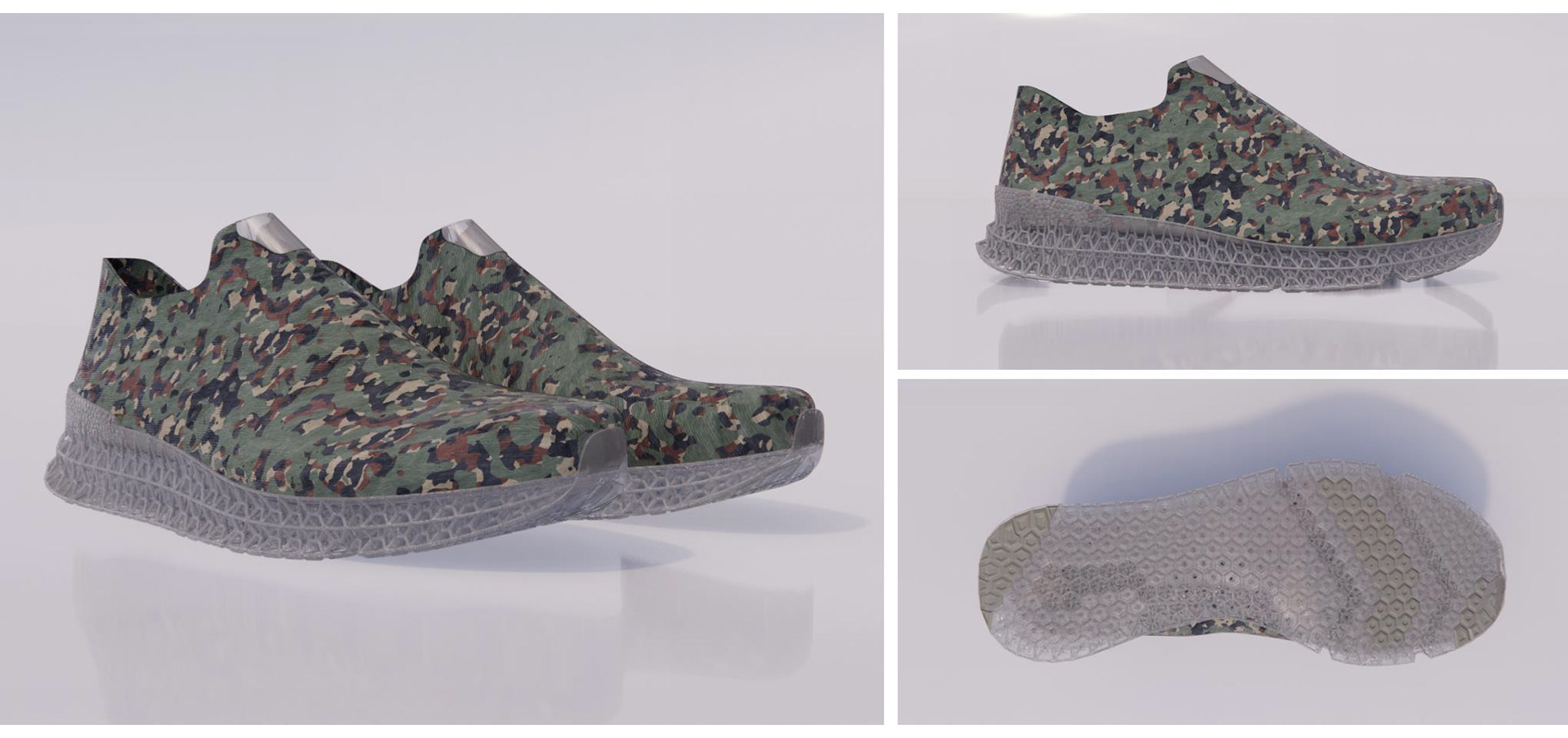
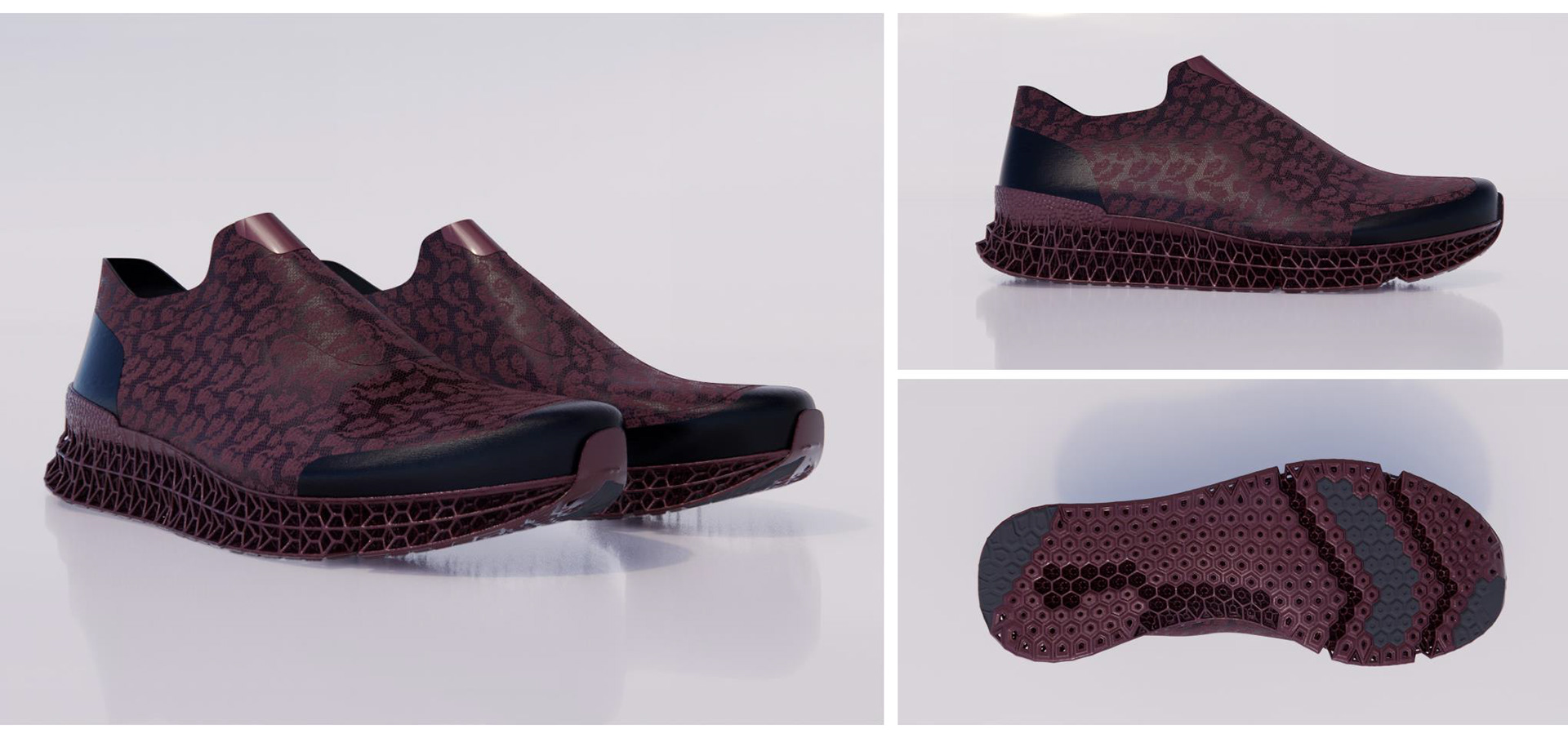