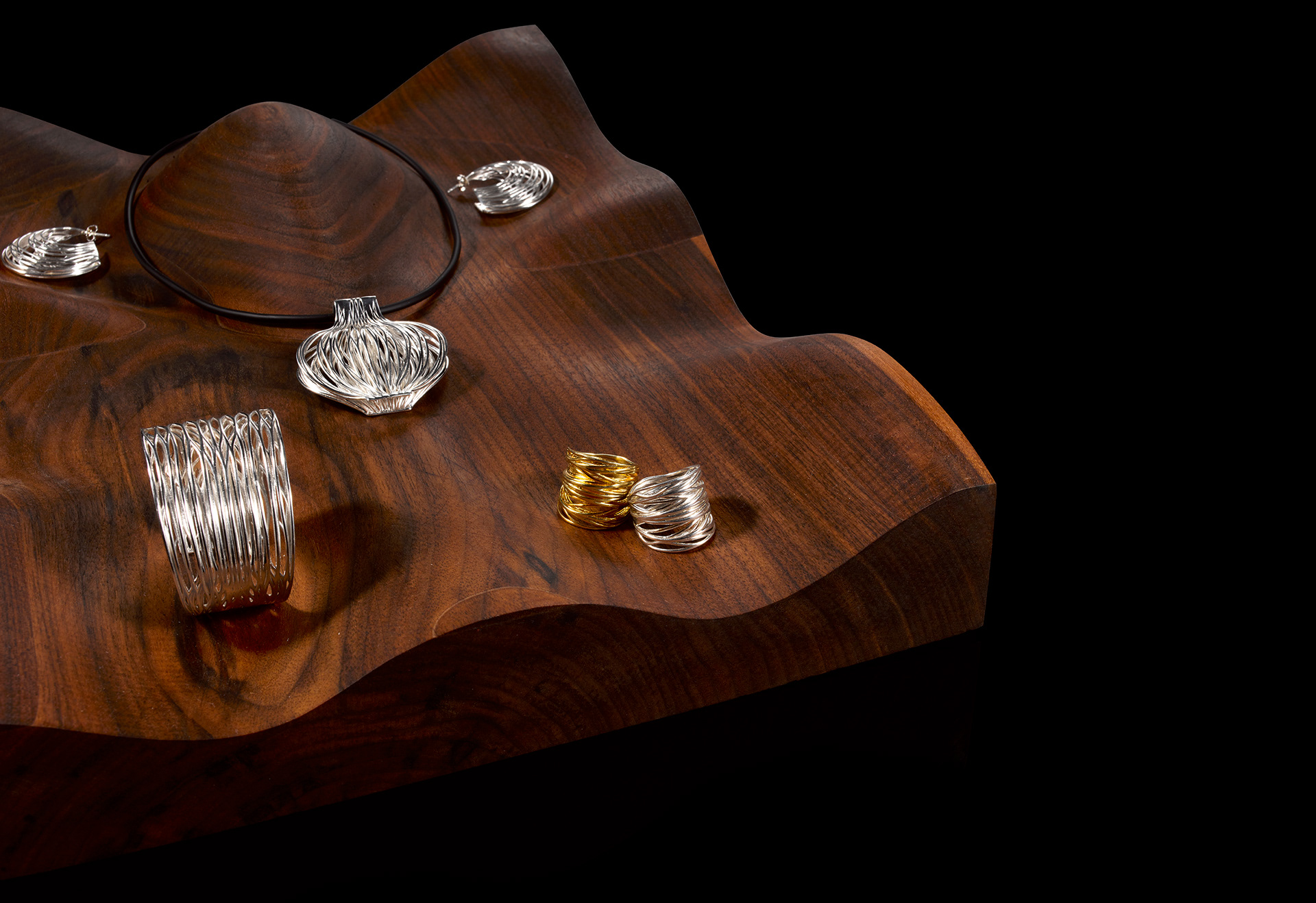
As a company sponsorship, Slicelab was taken into the residency program of Autodesk at Pier 9 that was geared toward designing four unique jewelry lines using 3D printing. These design explorations took inspiration from the ‘suspended weightlessness’ found in marine life. Analysis of delicate underwater creatures, such as jellyfish, was performed in an attempt to understand the body structures and movement patterns. Parametric software was used to mimic and interpret these such observations. As the first piece of hardware to come out of Autodesk, the Ember 3D printer was our primary focus. Constant material testing was done alongside operating large streams of rapid prototyping machines. With wax molecule infused UV polymer resins, 3D printed design pieces were directly used in the lost wax casting method.
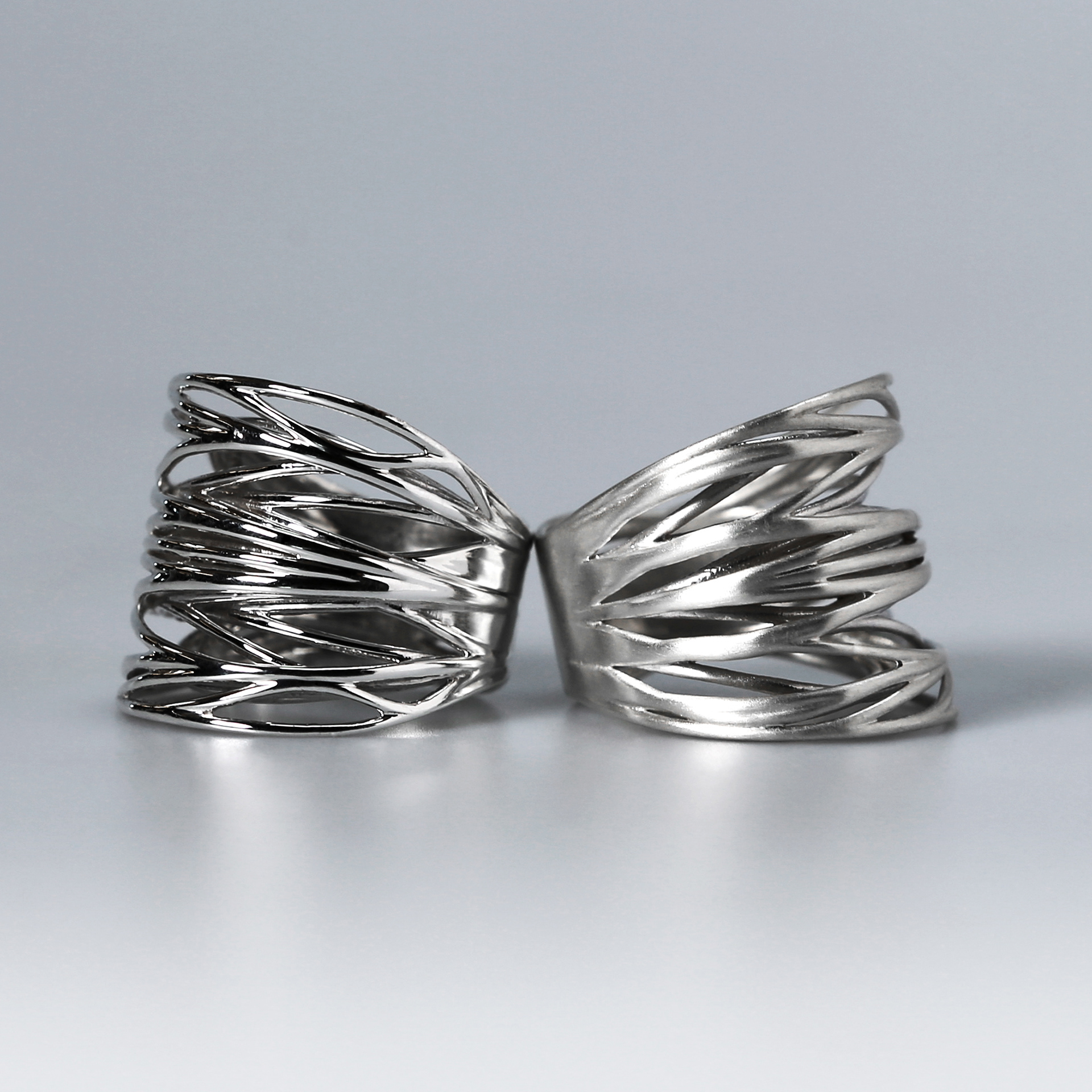
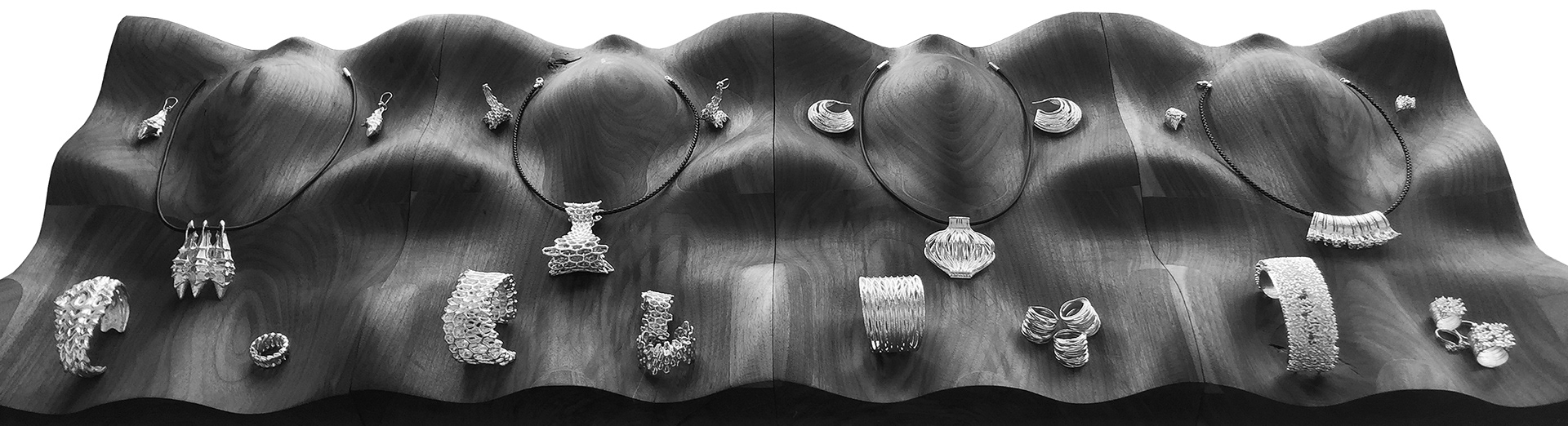
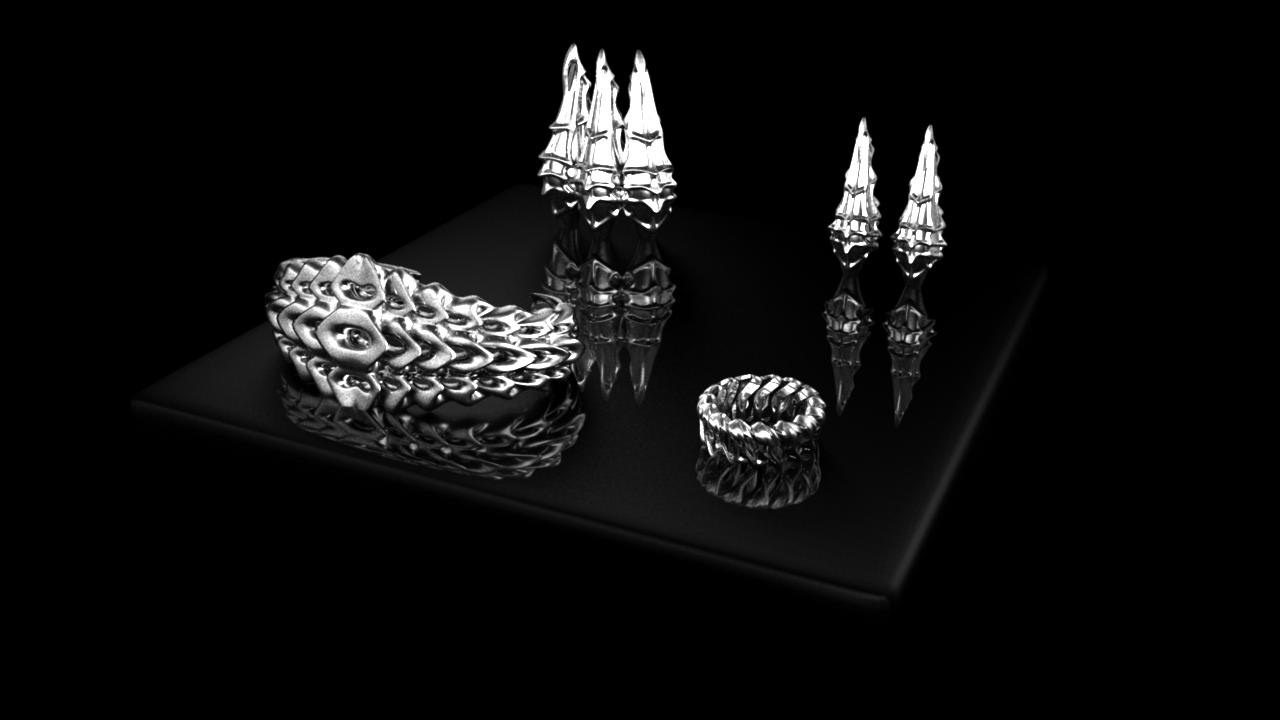
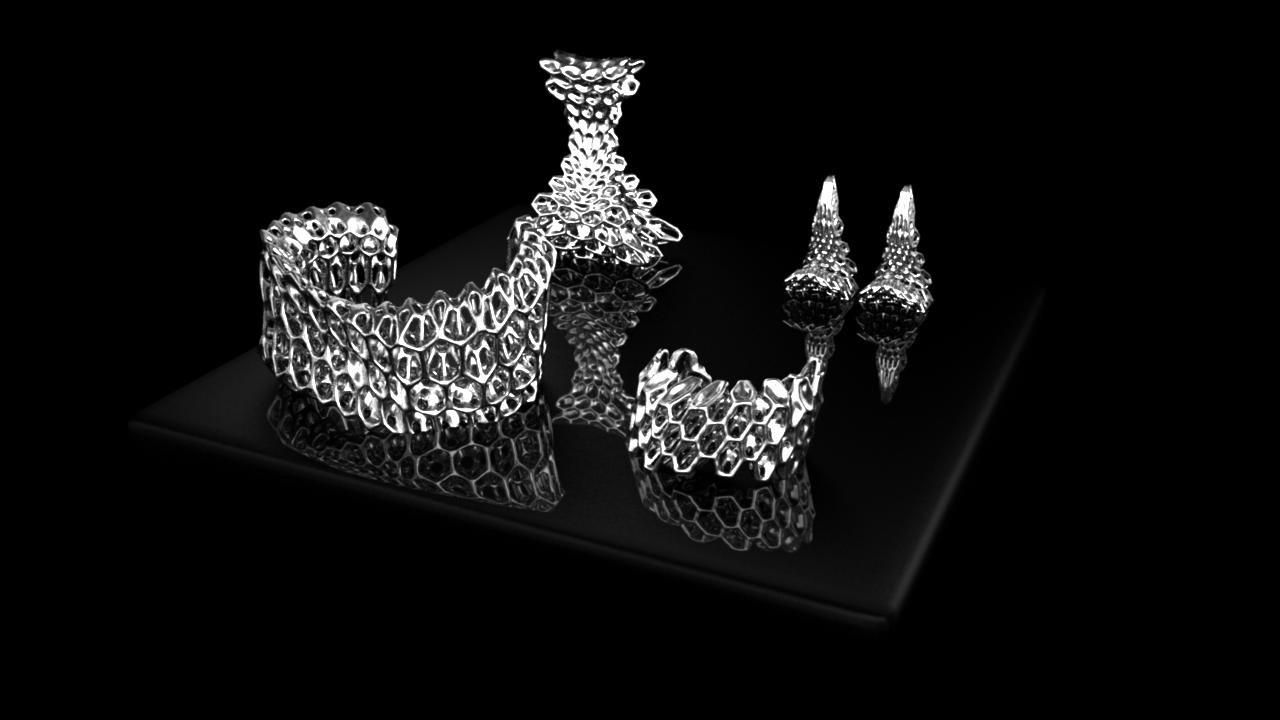
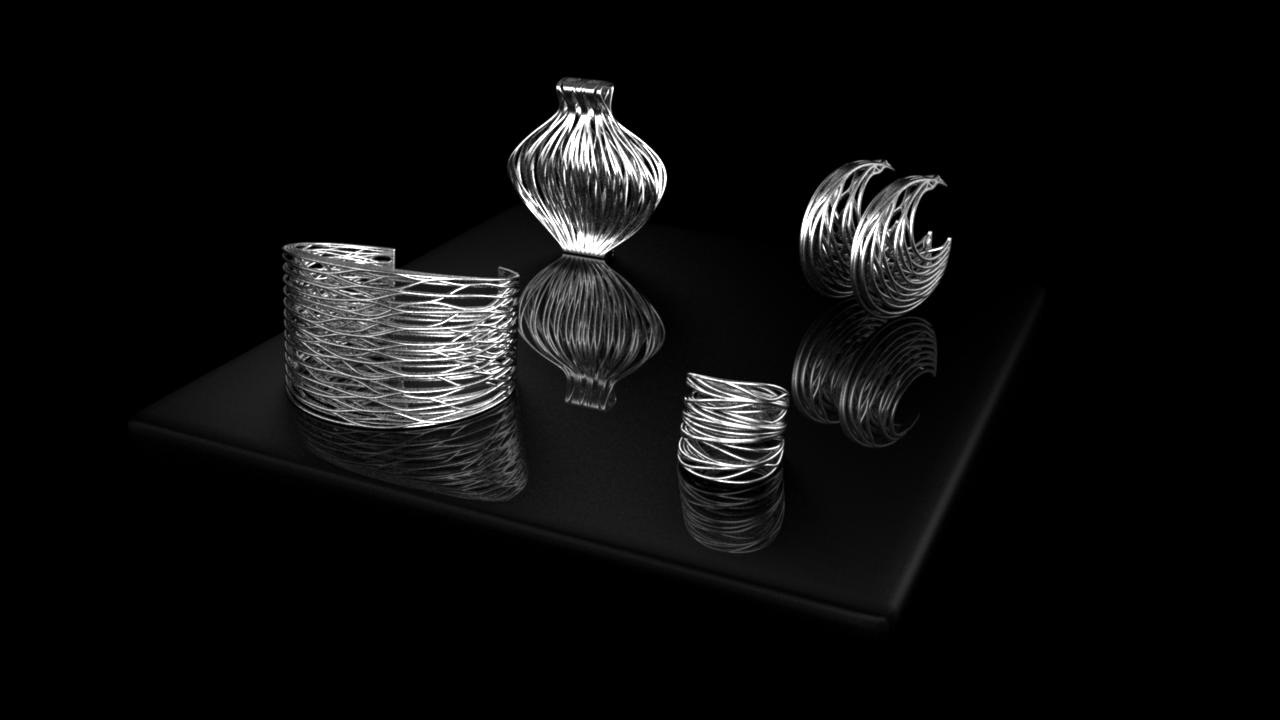
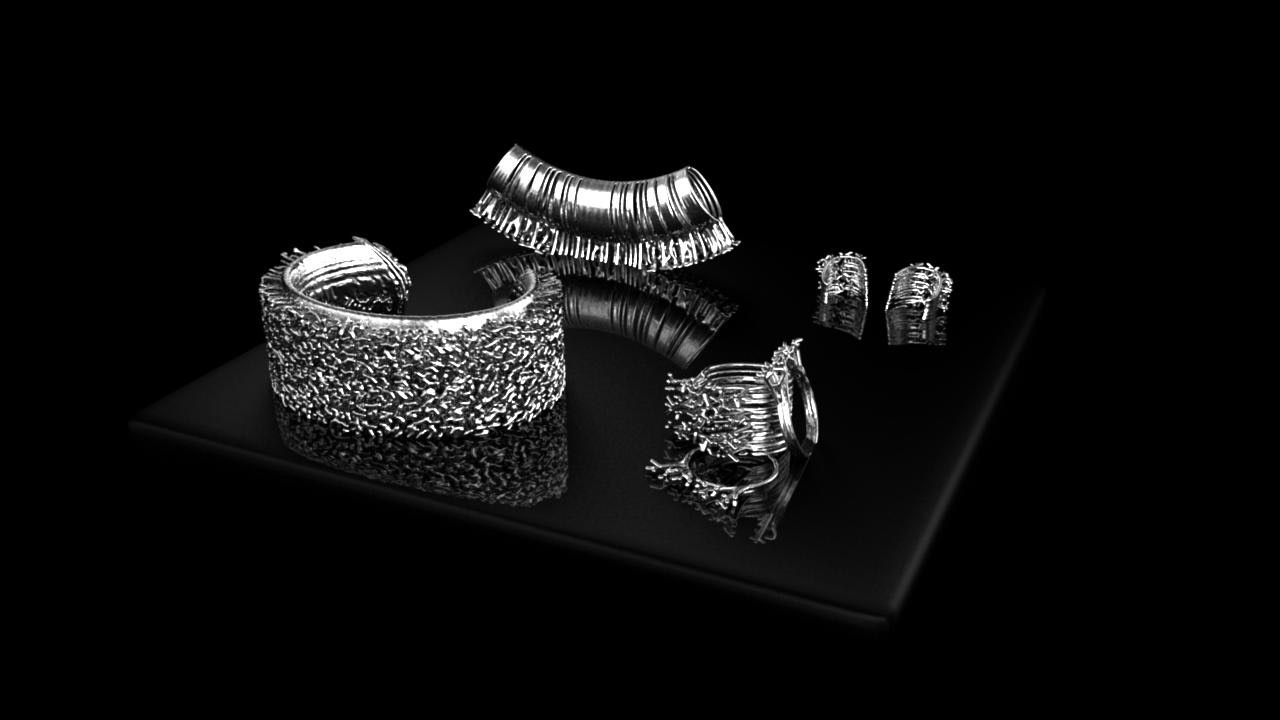
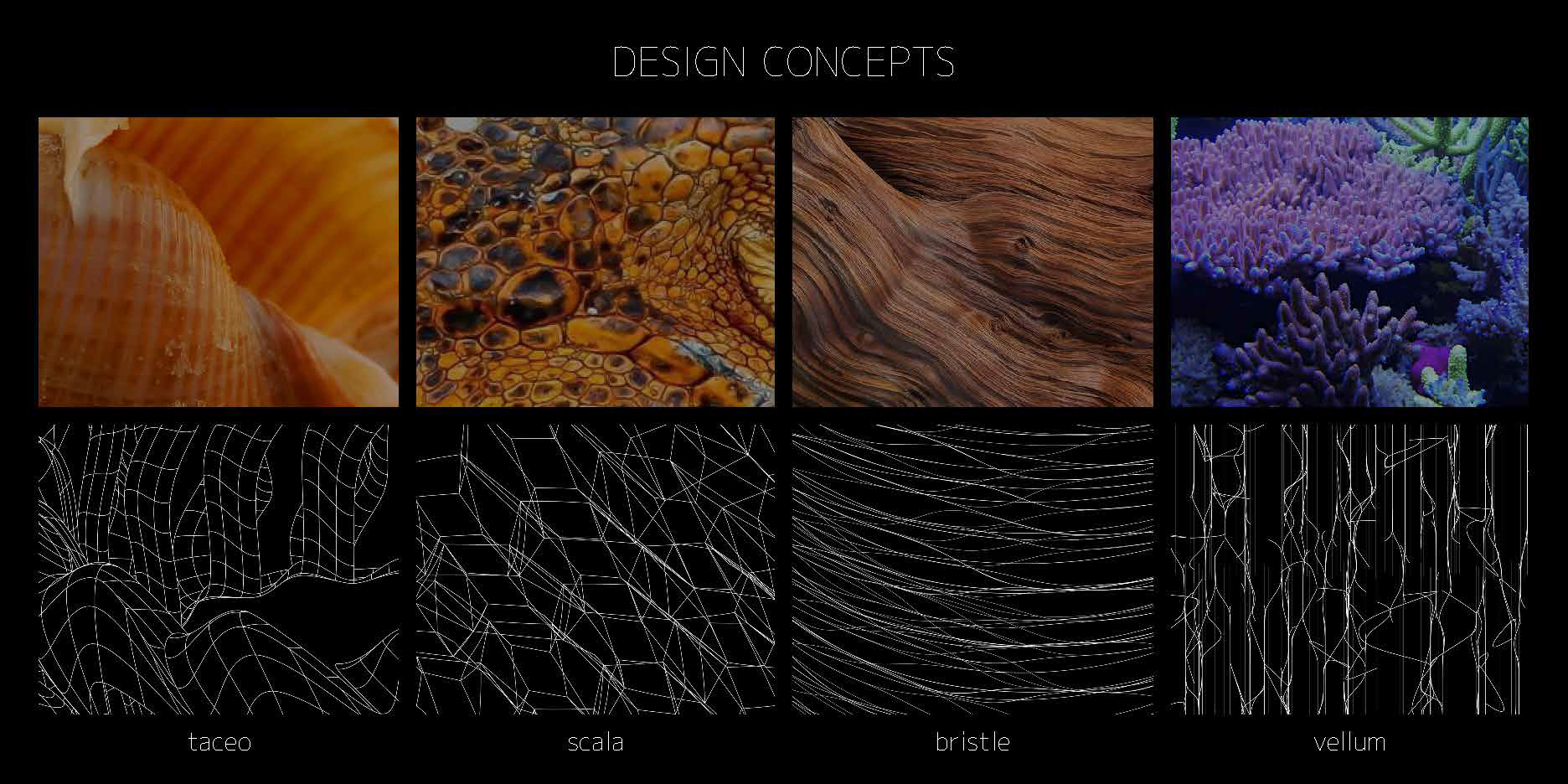
The marine life inspiration was translated into a set of linework studies that were later used to create volumetric models and ultimately 3D printed. Each line of jewelry had a cuff, a pendant, a ring, and earrings that shared a similar style of modeling and design aesthetic.
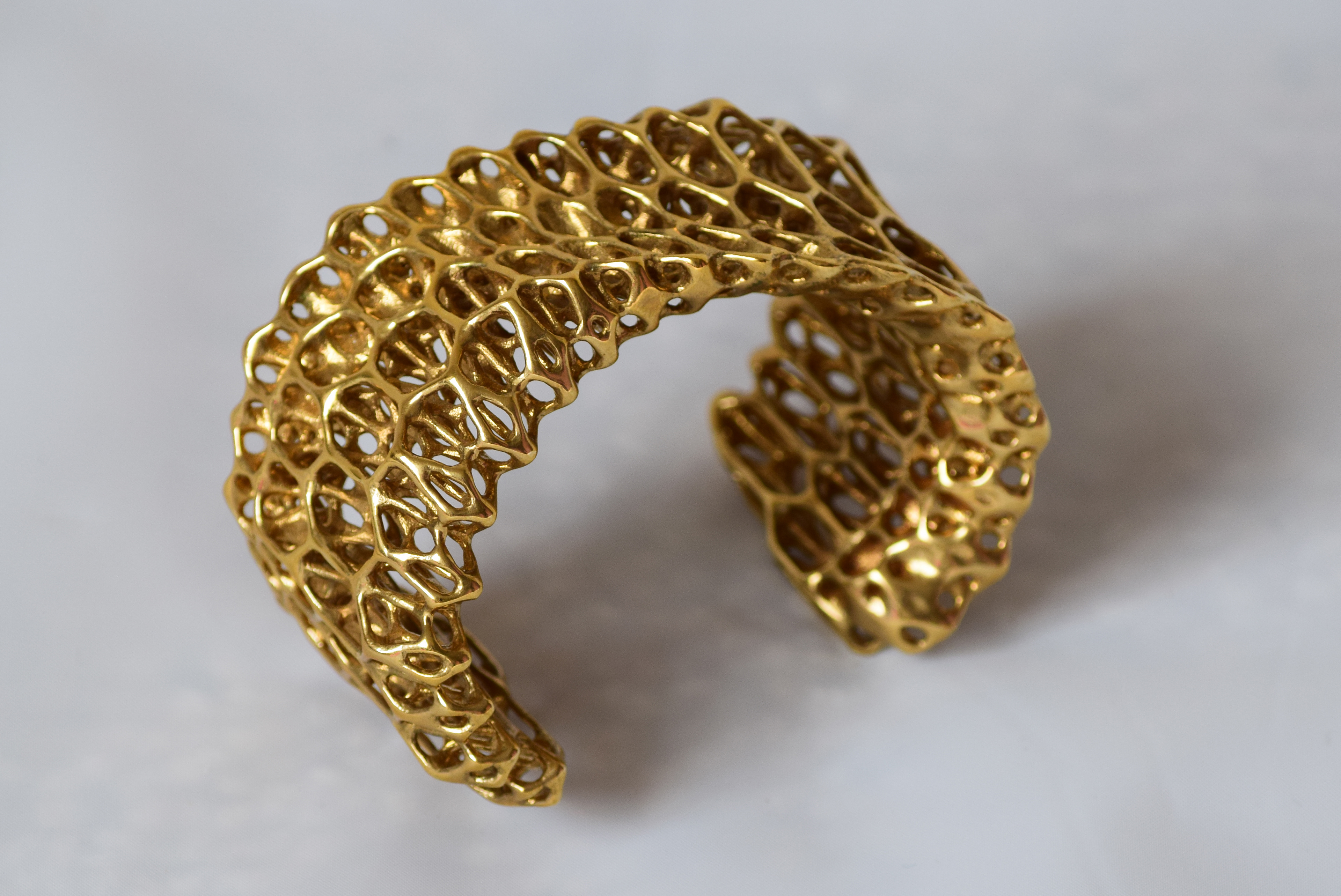
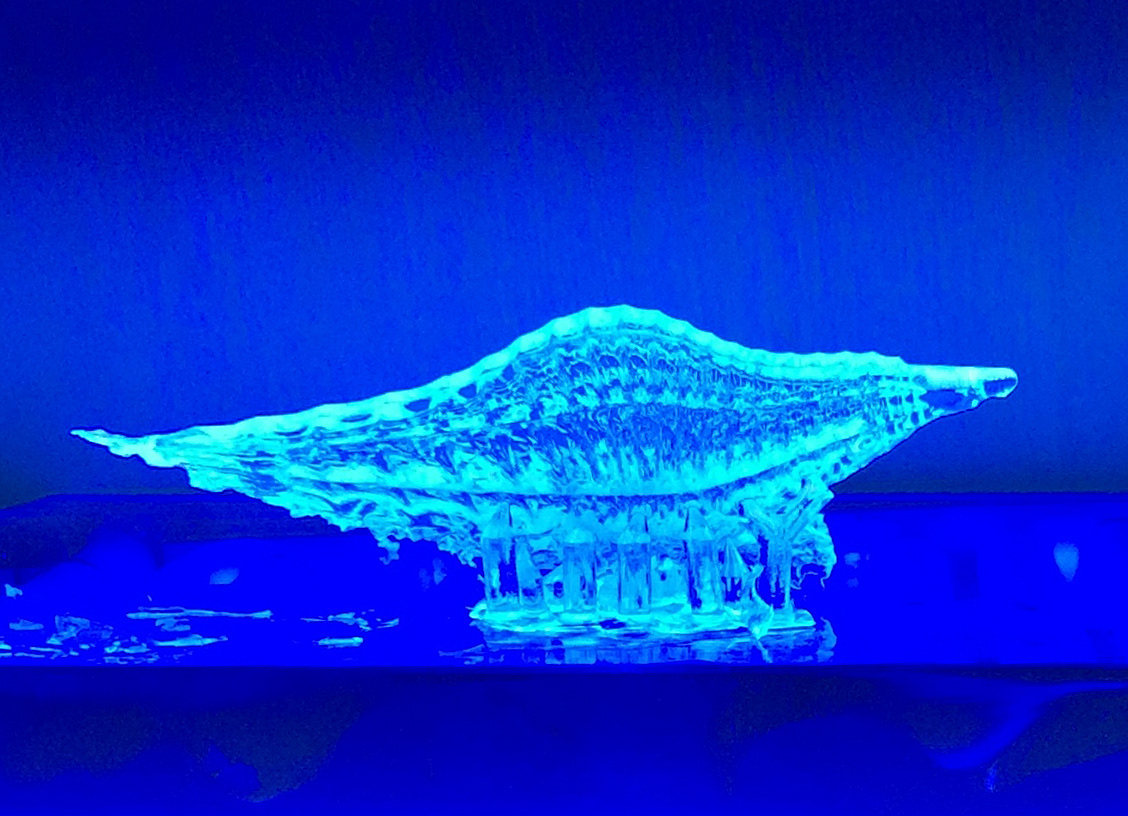
Throughout the residency, numerous resins ranging from flexible plastics to wax infused resins for casting were tested and iterated on by the material team. On a weekly basis, a new update in the chemical formula was made available to further feedback going through over 20 formulas. Additionally, using Autodesk’s Spark online platform settings needed to be adjusted constantly for optimal performance. The major limiting factors for successful prints came in perfecting the burn-in layer, separation slide velocity, model exposure, and first layer micron thickness.
In certain cases, additional accessories were integrated into the machine for better results such as this adaptable wiper blade. Keeping the print window clear and particle-free would be the main takeaway in achieving reliable print success. Clean resin flow within the material tray was studied while printing to see when and how prints failed.
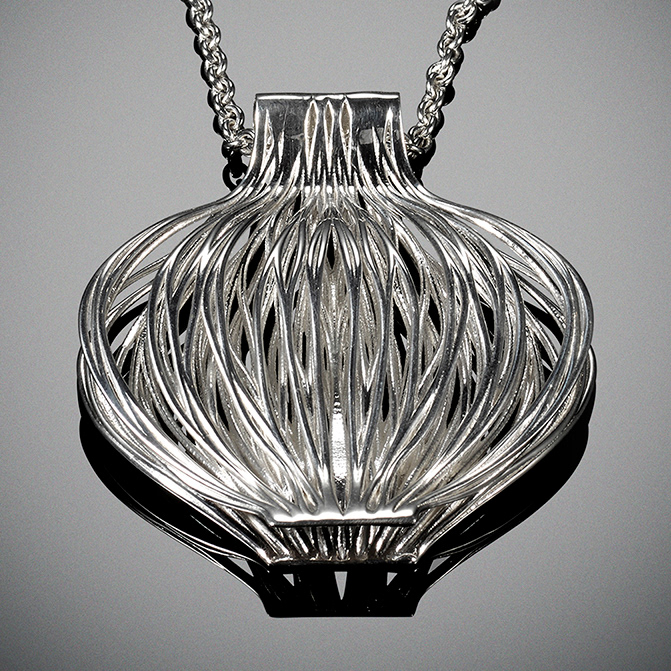
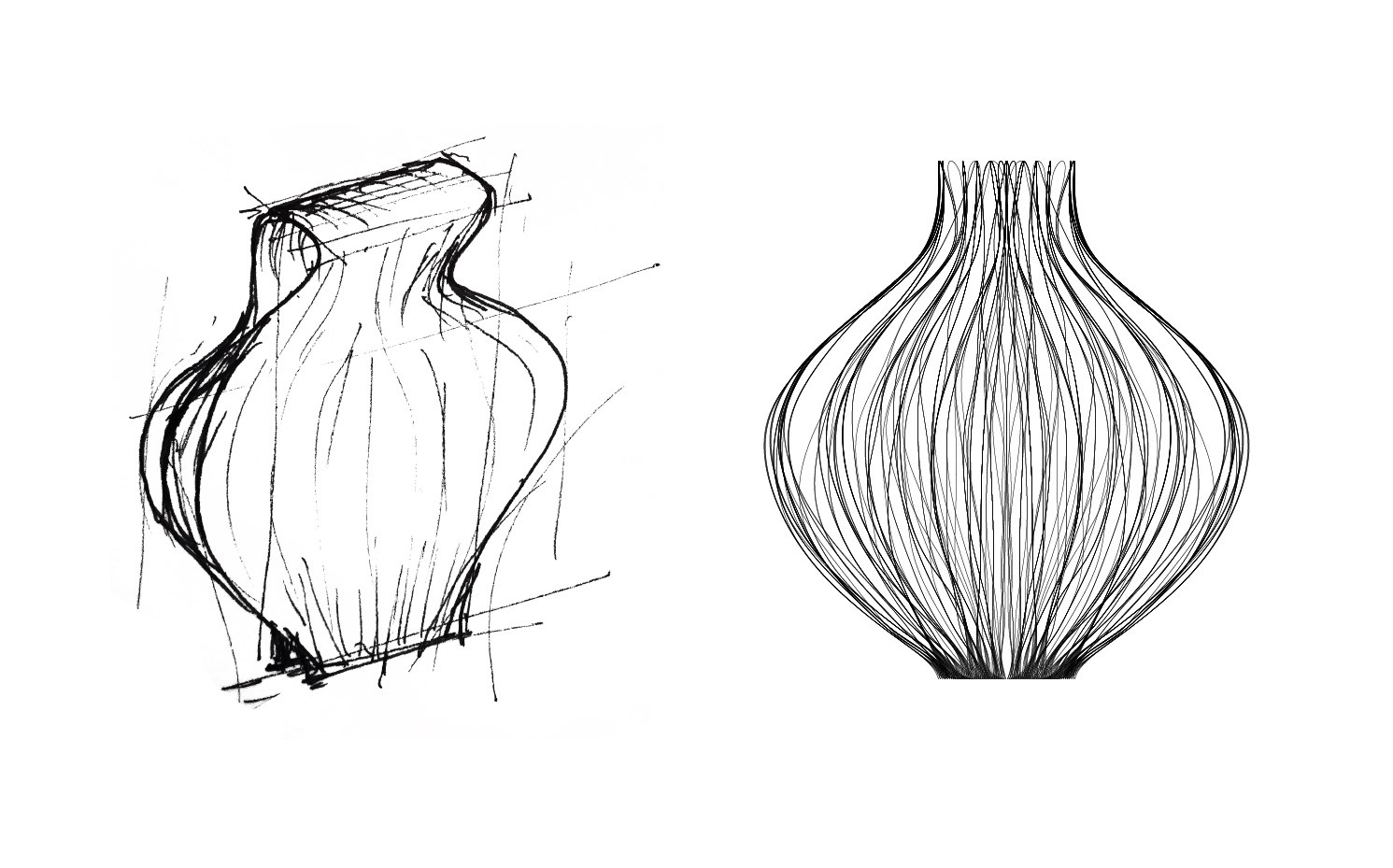
The precision in the printer was incredibly improved throughout the 4 months of the residency. UV light curing variations would also begin to play a large role in the casting stage of the project. Without fully cured resin, the prints would have trouble adhering to the casting tree within the flask in the burn-out process ultimately creating a failed cast.
Casting in fine powder investment, every detail on the cured resin would show. Due to the complex geometry that was designed, fully polishing the metals after casting would prove extremely difficult in the intricate areas. Therefore, it was crucial in having consistent, nearly perfect 3DP results. After the conclusion of the residency, the goal was to create a streamlined production of jewelry pieces as a case study to show future potential customers how to leverage this 3D print to cast process anticipating the release of the Ember.
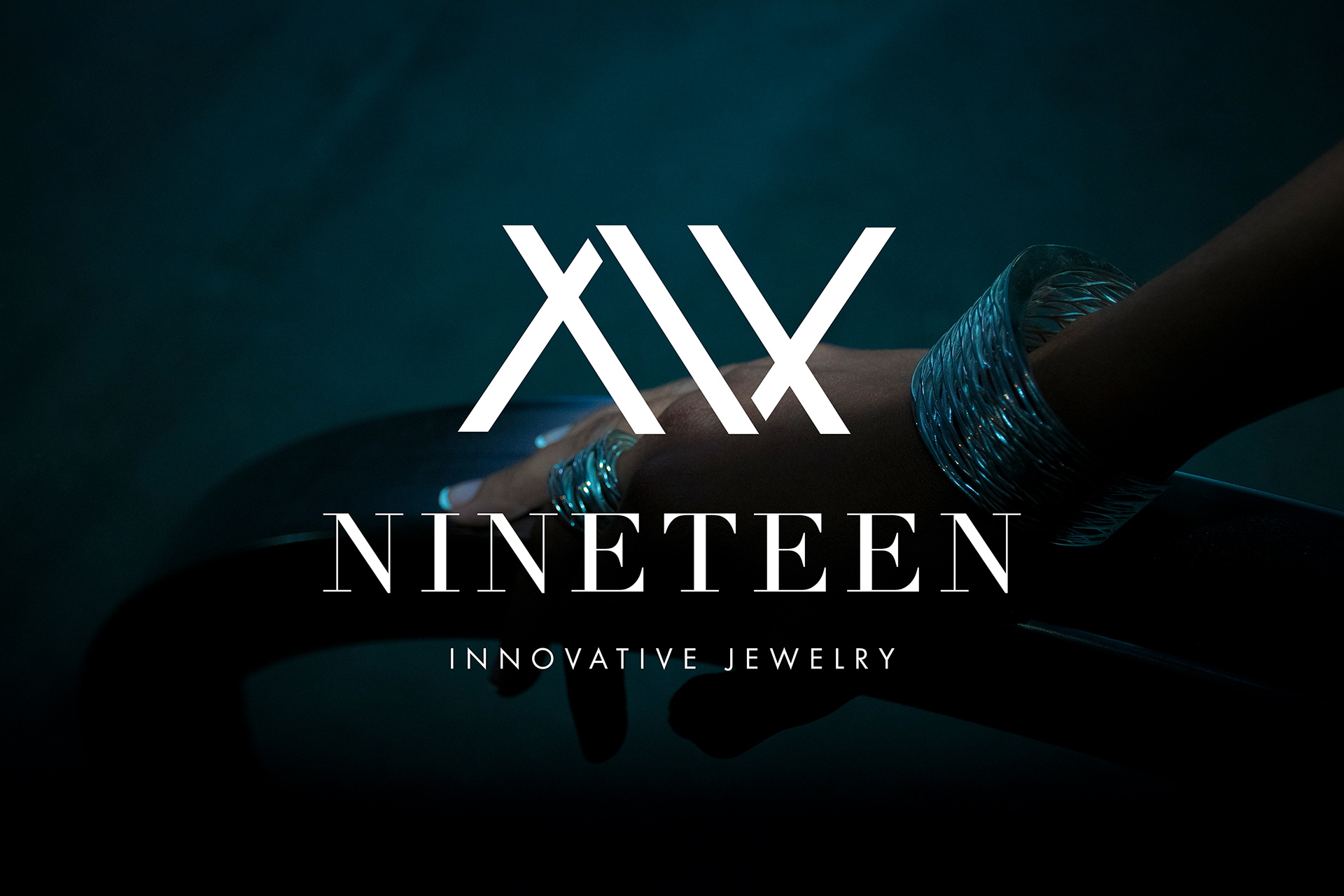
NINETEEN Jewelry was established as a separate entity of unique, sculptural jewelry that fuses an organic aesthetic with today’s top 3D printing processes. XIX uses the highest caliber of precious materials and technology through a distinctively evolved approach to contemporary design and wearable objects. The Nexus Collection is XIX’s breakthrough series of earrings, necklaces, rings, and bracelets inspired by a complex set of precise yet unpredictable lines found in the natural world. Paying homage to these organic elements, XIX simultaneously surpasses them; by designing intricately detailed structures that can only be realized through creative digital innovation.

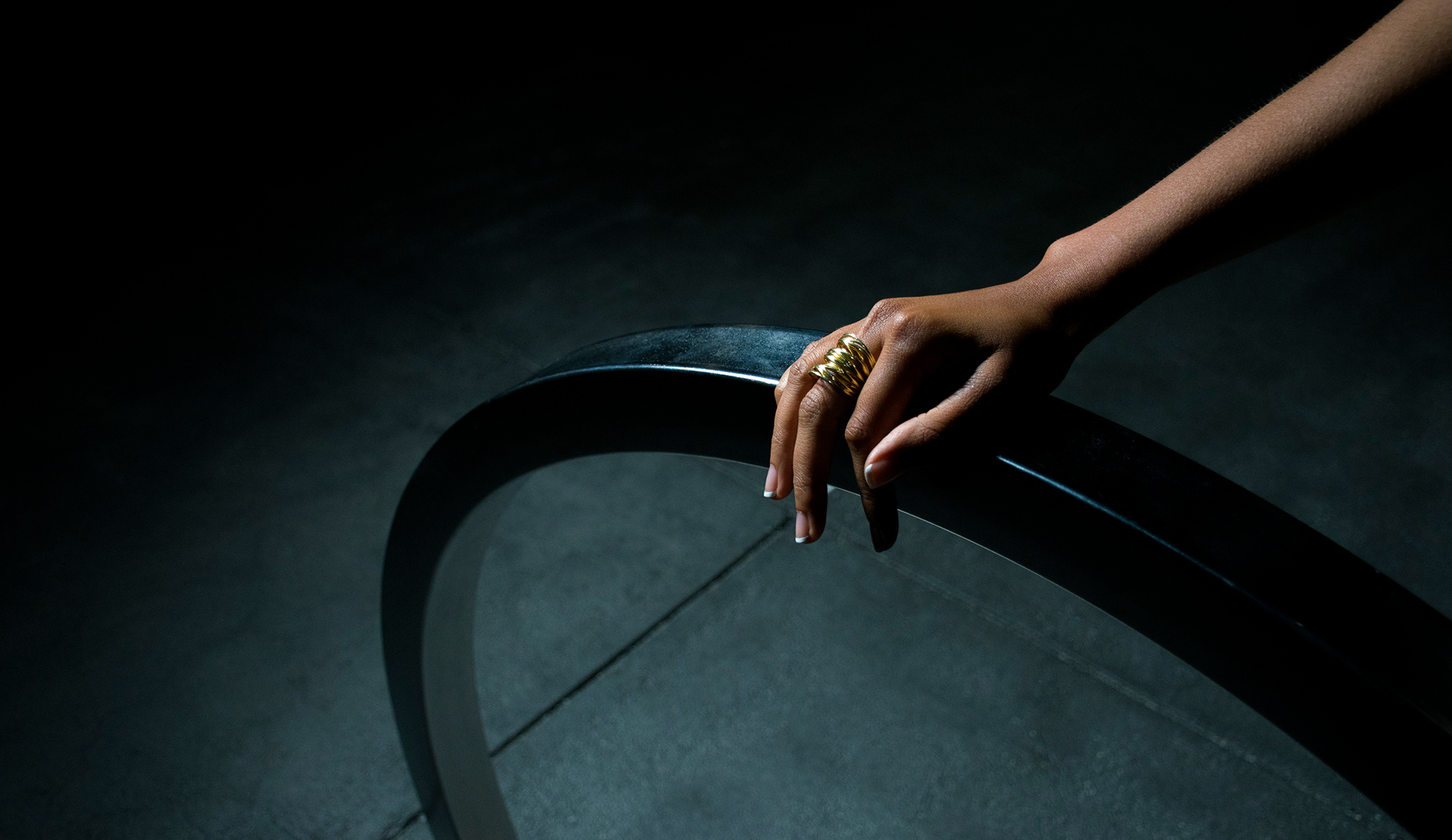
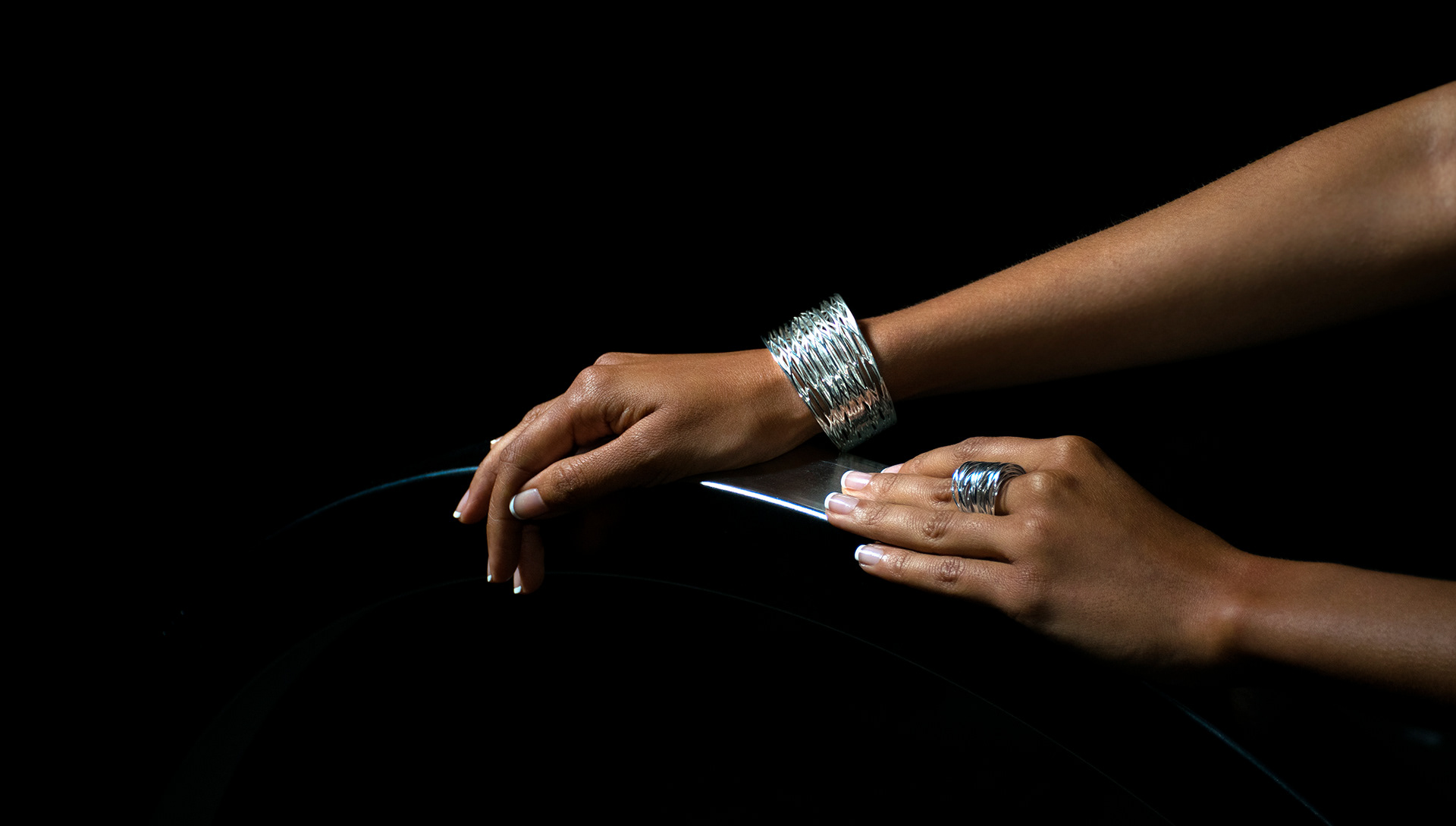
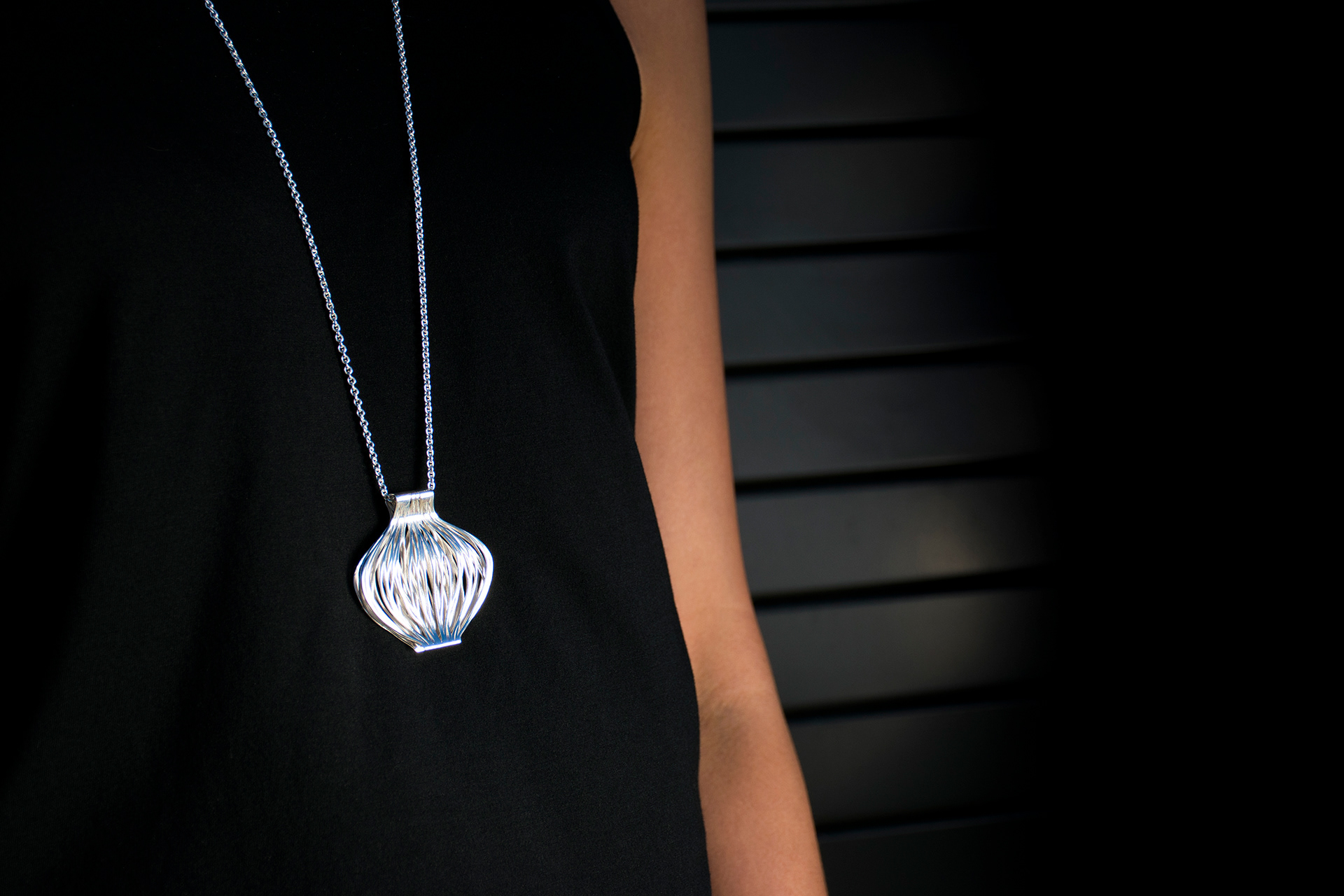
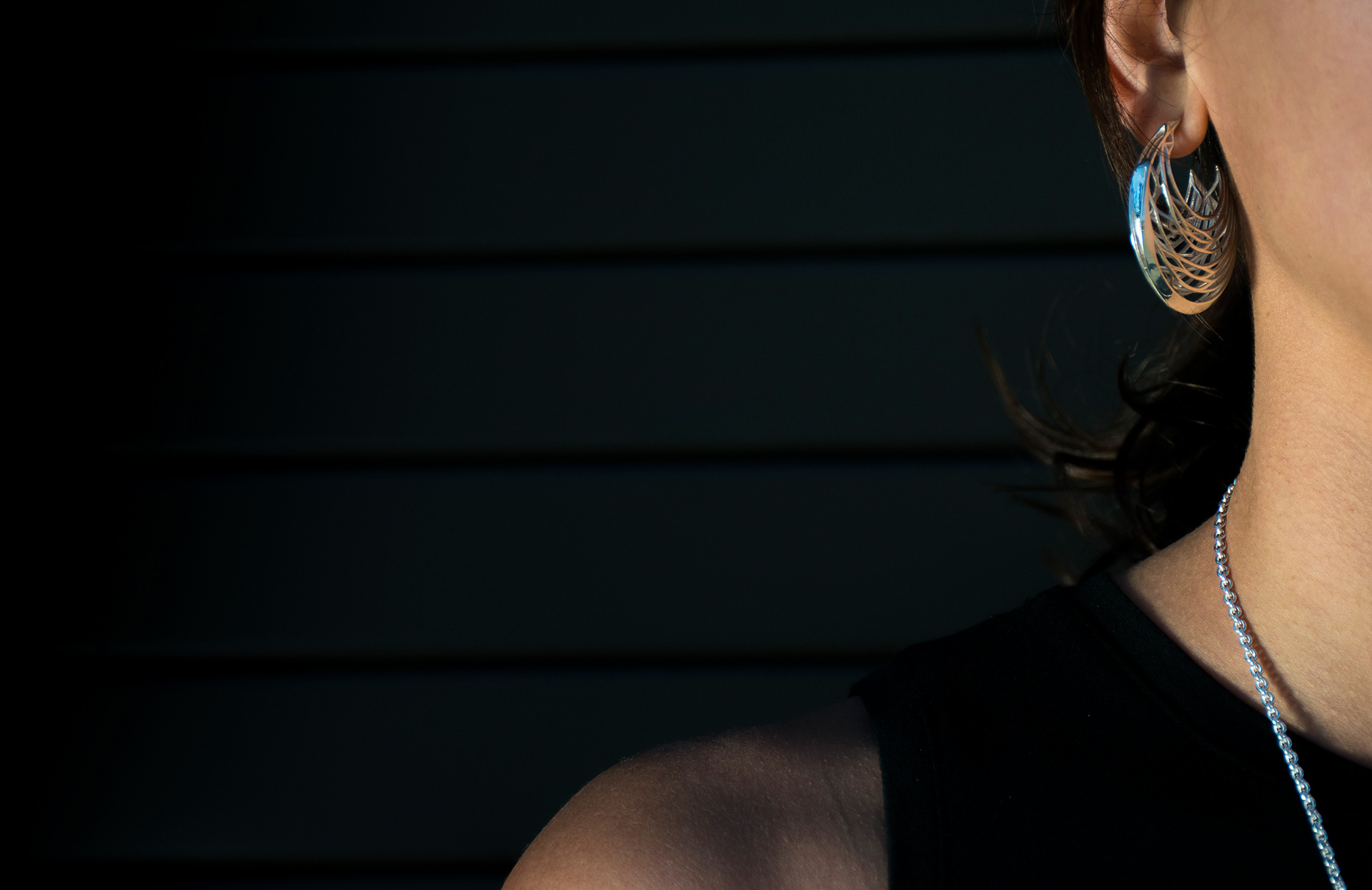
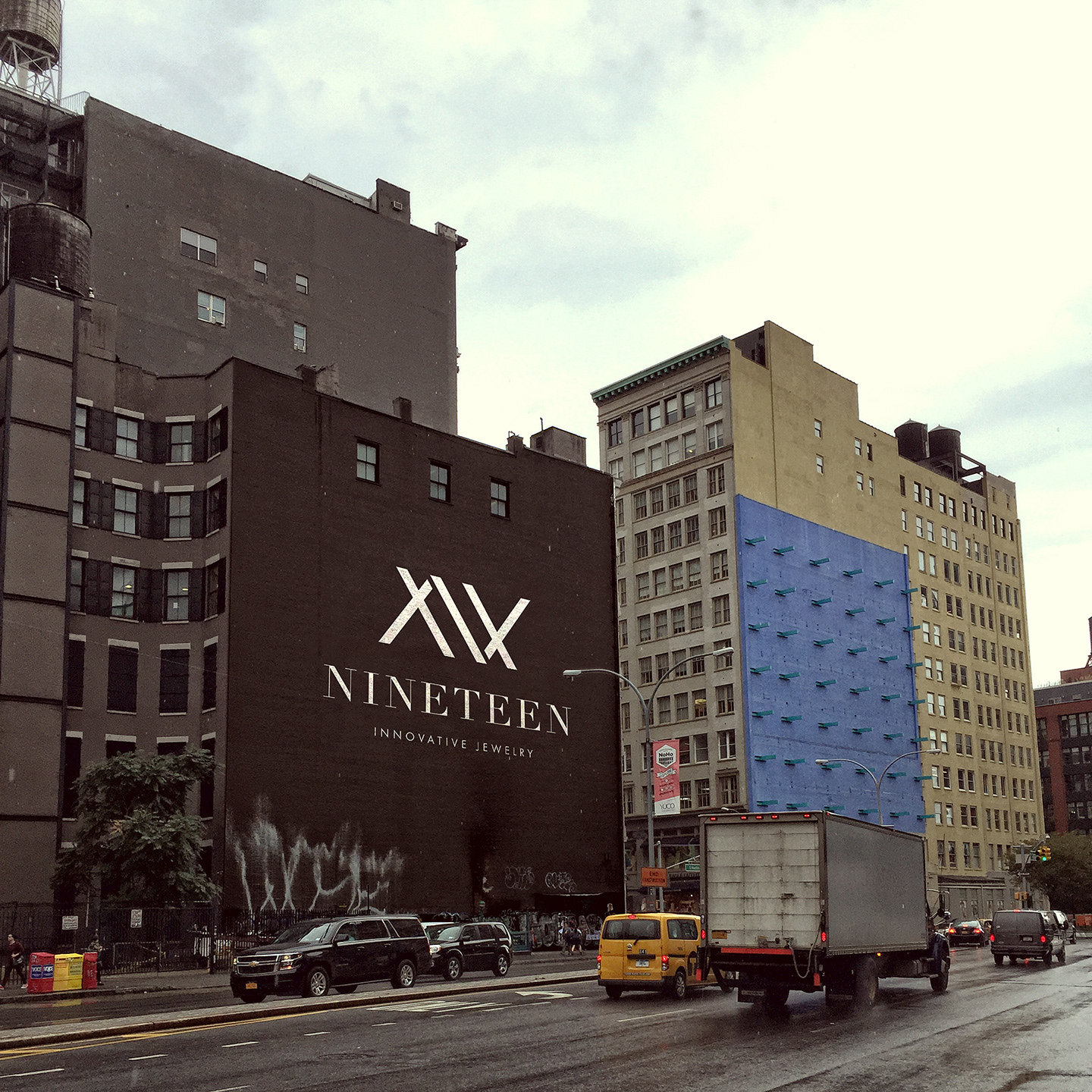
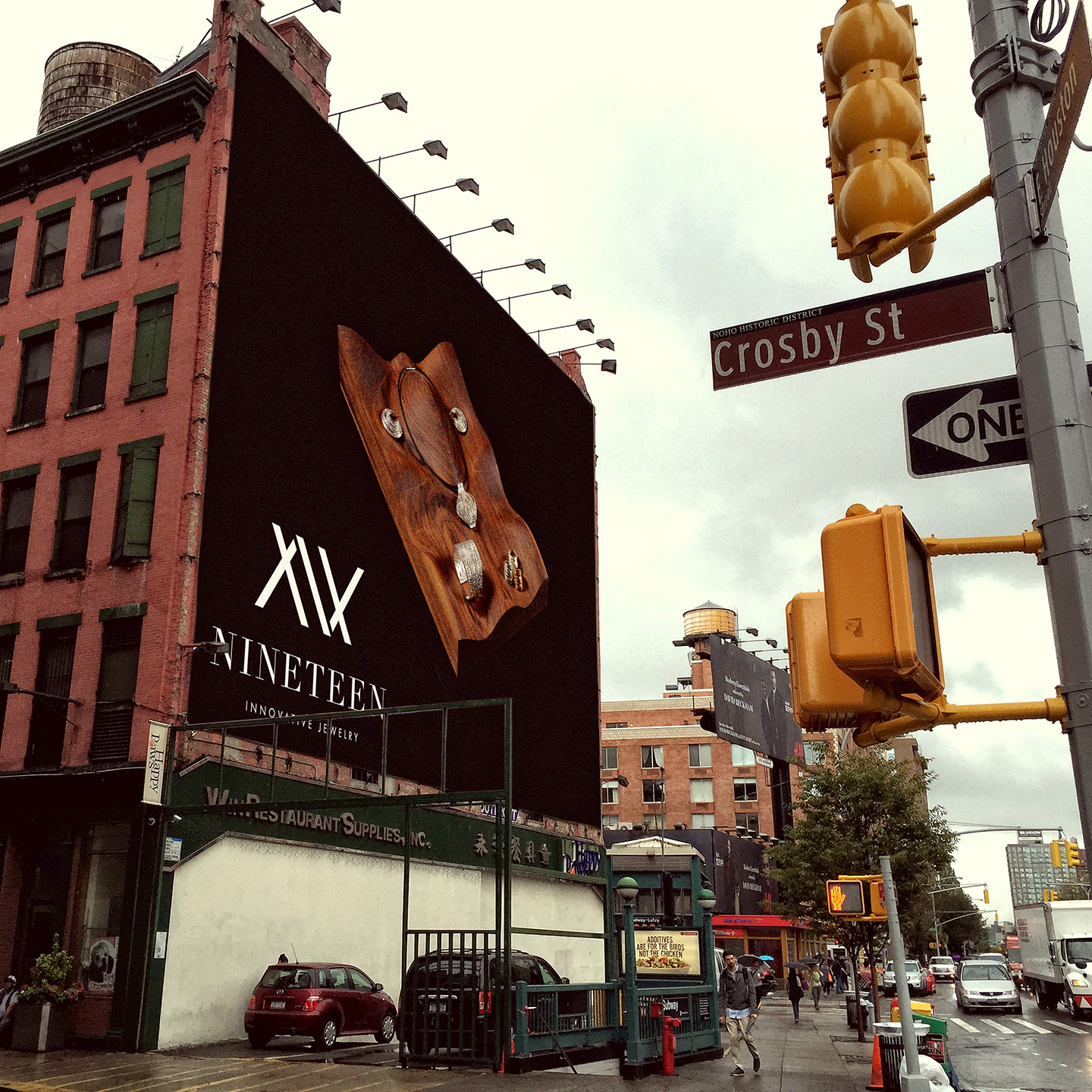
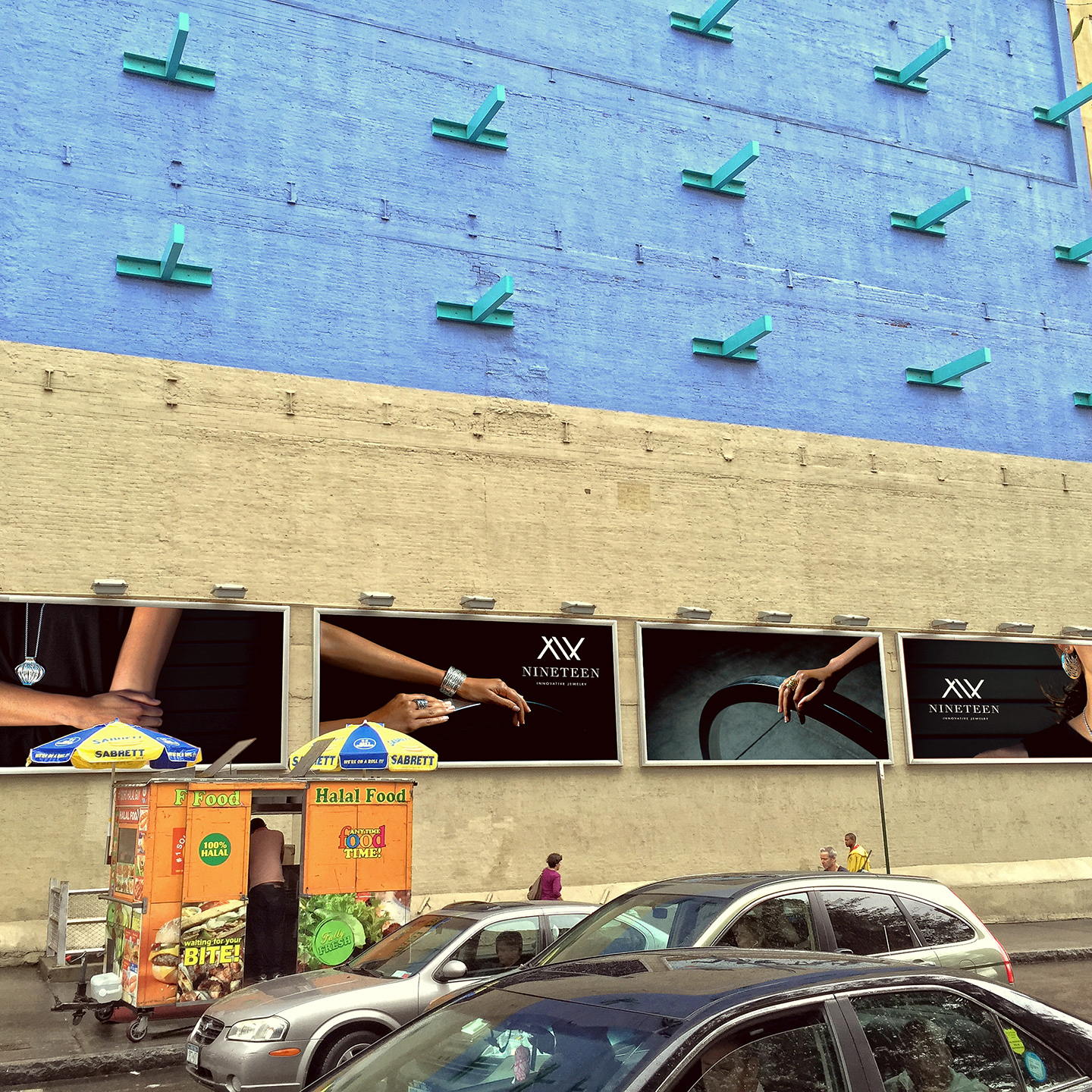
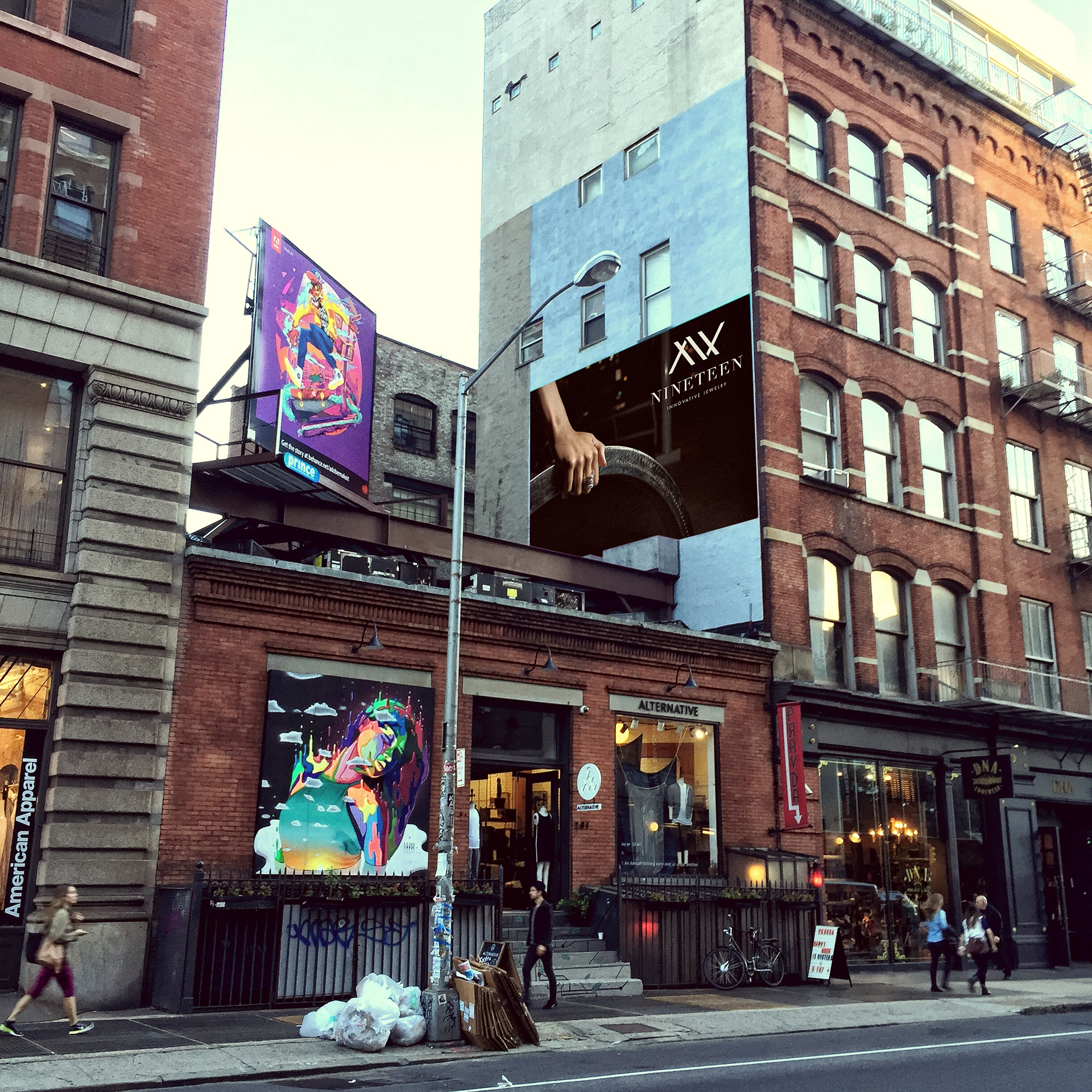
Process Images
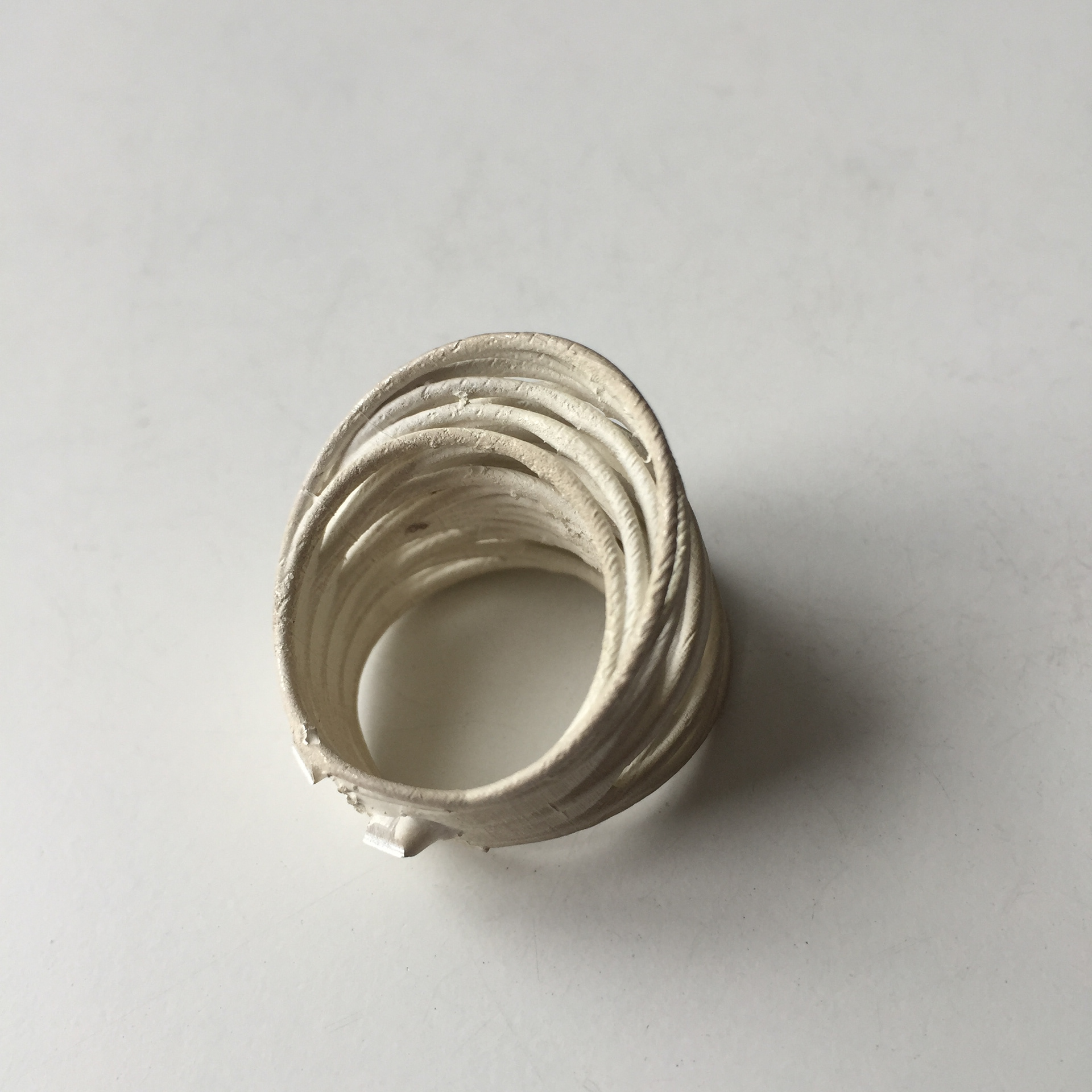
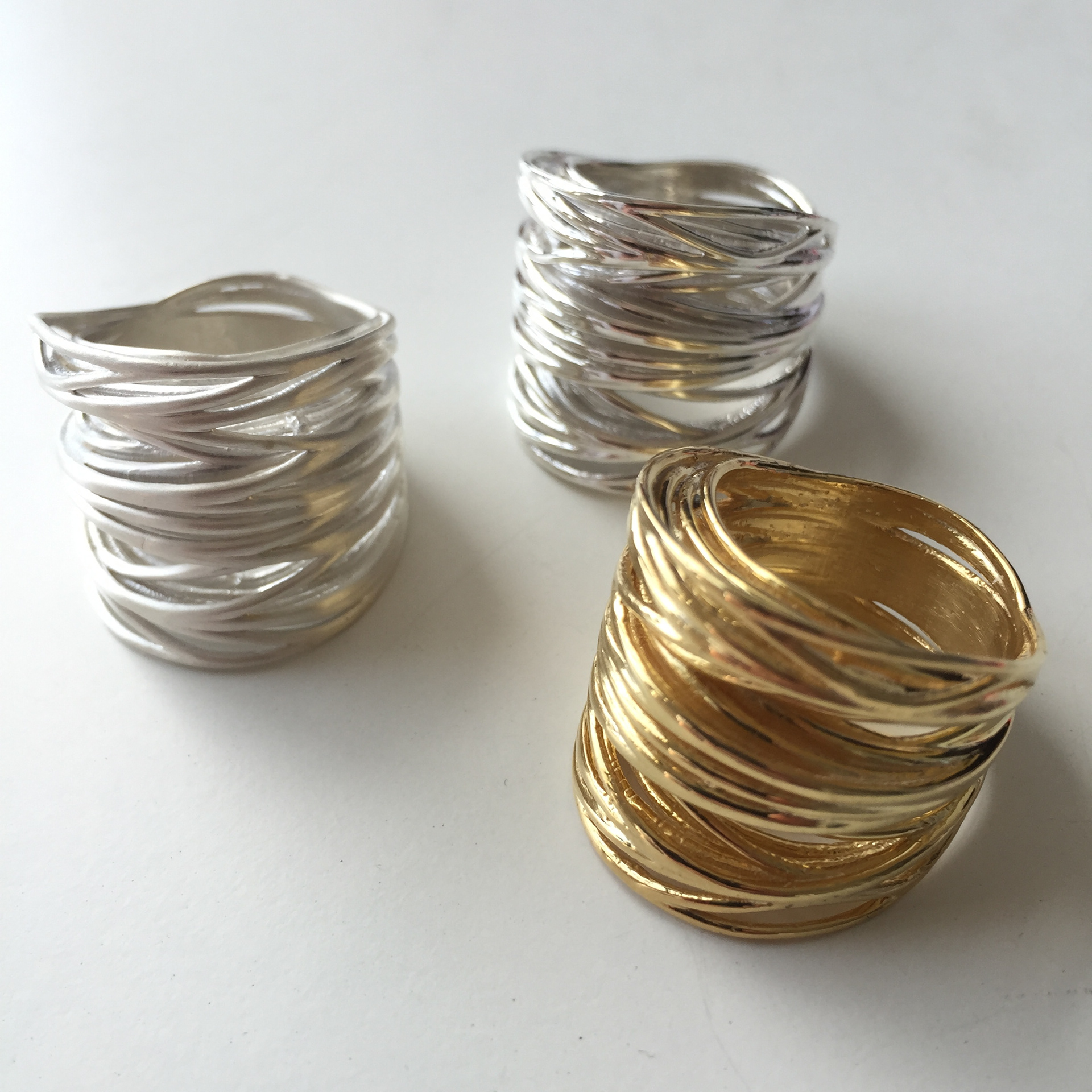